5 Benchmarks to Help You Measure Fleet Tech Performance
Paying attention to your fleet technicians and their output can help you streamline your fleet maintenance process and reduce downtime with faster, higher quality service.
Dec 6, 2021
6 min read
When it comes to fleet tracking, it can be easy to latch on to asset-based metrics – parts and inventory costs, total cost of ownership, utilization – but taking a moment to specify what to look for in your fleet maintenance tracking can be a huge boon for your operation as a whole. The best place to start? Your fleet technicians.
Fleet technicians are your frontline defense against downtime. When they work efficiently, they can create a seamless process from breakdown to work order to service completion and reduce the impact of repairs and maintenance. But if you’re not measuring their productivity in the right ways, you could be sacrificing valuable time on the road or worse, the quality of the services being performed.
We had a sit down with Chuck Metoyer, fleet manager at Abt, to chat about technician productivity, and we’ve outlined a few metrics you can use to measure performance, as well as a few tips from Chuck.
1. Hours Spent per Project
We’ve all heard that "time is money," and while the phrase is an age-old cliché, it certainly rings true in the fleet industry. Making sure that your techs are able to get vehicles in and out of the shop as quickly as possible – without sacrificing quality – can go a long way in avoiding downtime and maintaining profitability.
Because most techs work on an hourly basis, utilizing some form of time tracking is vital to understanding how their time is being spent in the shop. Whether you employ a simple spreadsheet or use service duration tracking in fleet management software, having that information lets you see which work orders demand the most labor and time investment.
Once you’ve got a consistent log of service hours, you can start categorizing service types, determine where your techs are spending the most effort and find ways to streamline or improve. For example, if you start to see more time spent on big, time-consuming repairs than on quick preventive maintenance, you might analyze your inspection process and PM schedules so that you can prioritize maintenance and lessen the amount of emergency repairs.
PRO-TIP FROM CHUCK: Compare each tech’s individual service times to analyze their strengths and weaknesses, and assign them work orders that cater to their strengths to optimize efficiency in the shop.
"There’s certain guys that you can’t give a diagnostic job… you know, trying to figure out a wiring issue. Each guy is different. You kind of get a feel for your guys after working with them for so long. You know what they’re capable of and what they’re not capable of."
2. Total Services Completed
While the time spent on a service provides some answers about tech productivity, the amount of service tasks completed asks another question entirely – how much is actually getting done from day to day?
It’s important to ensure that technicians are not only optimizing the time spent on services, but also addressing as many services as possible during working hours. Be sure to watch how many work orders are returned as completed each day and track their completion dates and times.
(Psst – Did you know that we have a section for tracking completion in our Fleet Maintenance Spreadsheet template?)
As you start to keep track of services completed for each tech, remember that part of the responsibility for efficient work days in the shop falls on whoever is assigning and administering the work orders. Using the average service times you’ve already established, if you expect a single technician to accomplish three high priority repairs in one day that take 4 hours apiece, you’re setting up the tech (and yourself!) for failure.
3. Hours Logged vs. Hours Worked
Similar to services completed, gauging how many hours your techs are logging versus how many they’re slated to work can give a better picture of shift productivity, as well as help you avoid having information slip through the cracks. If your techs work an eight-hour shift, but only log five, then they’re either not utilizing their time wisely, or they are inaccurately logging service hours, and both possibilities can create issues for your shop in the long run.
Once you start reconciling service logs, you can look for ways to encourage better productivity in the shop. For example, if you see a discrepancy in service hours, and your technicians tell you they’re having to spend a lot of time creating and completing work orders, you can find a solution, like using automated work orders in fleet management software, that can take some of the time strain off your techs.
PRO-TIP FROM CHUCK: Track services completed and set daily benchmarks, of course, but also remember to stay flexible.
"You can only do so much in a day, and I don’t want to go home beat up, so I try to just do what has to be done today, today and as much as can be put off tomorrow – if it can be put off tomorrow – let’s do it tomorrow. Don’t try to kill yourself to get everything done in one day; it’s impossible."
4. QC Failures
Fast service times and a good volume of work completed are great, but if vehicles are being sent back out onto the road without a solid quality control check, you run the risk of repeat services or even bigger repairs in the future. It’s important to not only have a good QC process in place, but also to have a record of when a vehicle fails a QC check.
Keeping track of QC failures lets you know how thoroughly your technicians are completing services – when a vehicle fails a QC check, it means that there was some level of deficiency in the service, whether in the diagnosis or the service work itself. As you see QC failures increase, it could mean that your techs require a little more training; or, if you see service times dropping too low, it could mean that techs are moving too quickly and need to take more time on services.
5. Repeat Service on a Vehicle
Most of your maintenance process should be structured in such a way that avoids repeat services – thorough work, good QC checks – but when repeat services do come up, it can signal a problem in the shop, or even with a vehicle.
Using software or a spreadsheet to keep track of any services on a vehicle can help you identify repeated services, as well as the technician that completed it. Then you can close the loop by talking to the technician to make sure the vehicle is being serviced correctly, as well as ensure that the vehicle itself isn’t suffering from a bigger issue that could be addressed by the manufacturer.
PRO-TIP FROM CHUCK: Incentivize accuracy and productivity with bonuses.
"Money talks, right? Around here, every employee is on a bonus fund. What we try to do is: If you do a good job, you get an additional amount inside your bonus. If you’re a person that doesn’t produce, you get less in your bonus. And you kind of use that number at the end of each quarter as a report card. It keeps the guys from thinking, ‘Eh, I don’t feel like working on this today. Let me just ship[this repair] out the door.’"
Experienced fleet managers like Chuck trust Fleetio to support them through implementation and beyond as they create a more productive environment for fleet technicians. Schedule a demo or sign up for a free trial today.
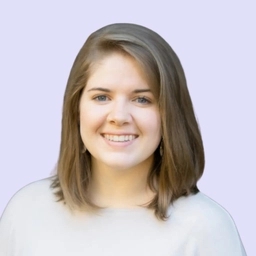
Senior Fleet Content Specialist
As a Senior Fleet Content Specialist at Fleetio, Peyton explores the voices and experiences that shape fleet operations. She focuses on how fleet professionals adopt technology, improve efficiency and lead their teams to bring clarity and context to the challenges happening across the industry.
View articles by Peyton PanikReady to get started?
Join thousands of satisfied customers using Fleetio
Questions? Call us at 1-800-975-5304