How to Improve Operations with Equipment Management Systems
Equipment management systems allow you to track and manage the tools and small equipment that help your business succeed. Managing equipment utilization and expenses in a centralized software maximizes efficiency and improves your return on investment (ROI).
Jan 12, 2024
9 min read

TL;DR: What is an equipment management system?
An equipment management system helps fleets track tools, reduce downtime, and cut costs by improving visibility, accountability, and maintenance.
Ways to improve operations with equipment management systems:
- Centralize equipment tracking: Use cloud-based software to monitor usage, status, and location in real time.
- Collaborate remotely: Mobile apps let teams report issues, leave comments, and stay aligned from any jobsite.
- Ensure safety with issue tracking: Flag faulty tools as out of service to prevent accidents and unauthorized use.
- Increase accountability: Assign tools to operators and track check-ins/outs to reduce loss and misuse.
- Optimize equipment usage: Analyze performance and service life data to identify underused or overworked tools.
- Control equipment costs: Log purchase prices, repairs, and resale values to evaluate ROI and plan replacements.
With the right equipment management system, fleets can boost efficiency, protect assets, and streamline operations alongside their vehicles.
What can fleets track with an Equipment Management System?
Many fleets, like landscaping and plumbing businesses, rely on a variety of small equipment to serve their customers. An equipment management system helps ensure your tools and small equipment are in safe operating condition to avoid downtime, accidents and costly replacement purchases.
Tracking equipment in addition to vehicles may seem like an overwhelming task. If you’re managing your fleet with paper and spreadsheets, it can be difficult to monitor assets in real time.
Equipment management systems make it easy to track all job-critical assets in a centralized software. With all information on a cloud-based equipment management system, you can monitor utilization, performance, conversations and issues specific to a piece of equipment to improve operations.
Lost tools equal lost time
When tools go missing, jobs get delayed and your bottom line takes a hit. Track your fleet’s tools and small equipment with a simple check-in/out system using Fleetio — so you always know where they are and where they’re going.
Start here6 Ways to Improve Equipment Management
Trying to figure out how to manage tools and small equipment can be challenging without an efficient equipment management system.
While some fleet managers only think about tracking vehicles, managing equipment is just as important to your fleet’s efficiency and bottom line. Here are six ways an equipment management system can help you track and improve your operation.
1. Collaborate with your team remotely
Because your team is often dispersed to different jobsites, leveraging an equipment management system maximizes visibility and enhances collaboration. Using a software that comes with an equipment management app enables you to track and manage your entire operation remotely.
Team members can leave comments on pieces of equipment or alert managers to any safety or maintenance needs. Not only does this keep you better informed, but collaborating on a mobile platform increases productivity and fosters a stronger connection with your team.
For Fleetio Users
Set your equipment operators up with an account in Fleetio so they can use the mobile app to let you know when they have any issues with equipment.
2. Leverage comments to get regular status updates on equipment
Monitoring equipment health is the best way to maximize efficiency and avoid downtime. Having operators conduct routine inspections and share their feedback as comments allows you to closely track equipment, ensure safe operating conditions, and identify any maintenance issues.
Paper inspection forms lack efficiency. They take longer to complete and require extra communication if an issue does pop up, often resulting in compounded issues and costly repairs.
For heavy equipment or construction equipment, managers can tailor inspection forms for all of their specialized tools and equipment. Having tailored inspection forms for large equipment allows your team to effectively communicate issues.
For Fleetio Users
While digital inspections are limited to vehicles and heavy equipment, you can send/receive comments and attach photos to tools and small equipment to keep track of the current status and surface potential issues.
3. Take action on issues to ensure fleet safety
Some fleets operate dangerous tools and small equipment to complete tasks. Mitigating risks and ensuring safety is paramount. Implementing safety procedures and maximizing asset visibility is the best way to stay informed of issues and keep your team safe.
Whether issues are identified immediately during inspections or on the jobsite, managers must communicate issues quickly. Equipment management systems provide increased visibility across your operation and allow you to communicate issues with your team. Managers can view and update equipment status in cloud-based software to inform others of potential safety issues.
Since broken equipment may have to stay in the vehicle until it can be fixed, consider creating a sticker to label equipment as unsafe.
For Fleetio Users
When an issue arises, use the equipment status field to mark a piece of equipment Out of Service. This prevents team members from checking out the equipment until your tech is able to inspect and repair the issue.
4. Keep a usage log and improve accountability
While tools and small equipment may not seem expensive compared to larger mobile assets, acquisition and replacement costs add up over time. Fleet managers can assign equipment to certain operators and ensure equipment is properly maintained, without having to physically inspect it. Equipment assignments create an audit trail for each piece of equipment and hold team members accountable.
Without accountability, small equipment and power tools can often go missing or take unnecessary abuse due to carelessness. By tracking use across your team, it's easier to look into the cause of certain problems or identify the last person to use a piece of equipment before it went missing.
For Fleetio Users
Use barcodes or NFC tags to create a simple system for checking equipment in and out. View the Assignment History to see usage. Attach equipment to vehicles within Fleetio to keep a record of last-known locations.
5. Track equipment utilization and condition
By analyzing utilization reports in your software, you may notice you’re over-utilizing certain equipment, causing it to wear out quickly. From there, you can determine whether to add new equipment or potentially find under-utilized equipment in your current stock.
Tracking utilization in an equipment management system provides insight into how your tools are used. This data can help you keep track of preventive maintenance, develop strategies to lengthen equipment lifespan and estimate when equipment should be replaced.
For Fleetio Users
Use the Estimated Service Life field to set expectations around the time in service for a piece of equipment and determine whether or not your equipment is being over or under-performing according to the expectation.
6. Monitor expenses to ensure profitability
Controlling fleet expenses across your operation is a balancing act. While vehicles may take up a large part of your budget, managing equipment expenses is just as important.
An equipment management system allows you to input how much you spent to purchase a piece of equipment, as well as the anticipated resale price. Attach documents of any additional parts, warranties or service performed on the equipment for easy reference when necessary.
See how J. Pettiecord construction manages equipment
By having this information readily available the next time you go to replace a piece of equipment, you can see if the anticipated resale value and lifespan align with the actual records in order to determine if specific equipment types or brands are falling short of expectations.
For Fleetio Users
In addition to the equipment Purchase Price and Estimated Resale Value, you can attach documents and comments within a piece of equipment to keep a digital record of all expenses incurred over the life of the equipment.
Finding the right equipment management solutions for your fleet
As your fleet operation grows, you need a system that allows you to track all of the assets that allow you to perform the job effectively. A few things to look for in a good fleet management system include a:
- digital record of usage
- status field to communicate service needs
- mobile equipment management app
- communication workflow to track comments
- process for keeping up with equipment location
- system for reporting and tracking issues
Fleetio's equipment management system has all of that and more, right alongside the same system you use to track your fleet vehicles. Eliminate multiple logins and simplify your equipment management, tracking and communications with Fleetio.
Keep your tools and equipment on track
Stop searching for tools or missing equipment. Fleetio simplifies tracking, so you always know what you have, where it is and who’s using it. Let’s show you how it works.
Schedule your live demoFAQs
What are examples of equipment management systems?
Equipment management systems range from paper logs and spreadsheets to software solutions. While manual methods can work, they’re prone to errors and inefficiencies. Software like Fleetio centralizes asset tracking, maintenance schedules and reporting, improving accuracy and productivity.
What is an equipment management list?
An equipment management list is a record of all assets, including names, serial numbers, locations, maintenance history, and condition. Keeping this list updated helps improve accountability, optimize asset usage, and reduce downtime, especially when managed through software.
What is an equipment maintenance system?
An equipment maintenance system tracks, schedules and manages maintenance to reduce downtime and extend asset life. It automates service reminders, logs repairs, and monitors equipment usage. Fleetio, for example, streamlines preventive maintenance, work orders, and inspections in one platform.
What is an equipment management plan?
An equipment management plan outlines how a company acquires, maintains and disposes of assets. It includes tracking, maintenance schedules, inspections and replacement strategies. A well-structured plan improves uptime, controls costs and ensures assets stay in top condition.
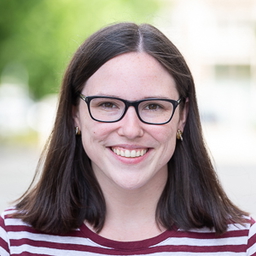
Content Marketing Specialist
Laura Flowers is the Content Marketing Specialist at Fleetio. When she’s not blogging, you can find her reading on the couch with her cat or in the studio tap dancing.
LinkedIn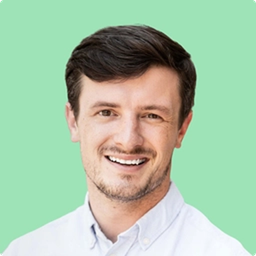
Director of Fleet Content, Fleetio
Zach Searcy is the Senior Content Marketing Manager at Fleetio with more than 5 years of experience in the automotive and fleet industries. His content creation days started in middle school when he and his friends began filming lightsaber battles to upload to a new website: 'YouTube.'
LinkedIn|View articles by Zach SearcyReady to get started?
Join thousands of satisfied customers using Fleetio
Questions? Call us at 1-800-975-5304