Guide to Creating & Optimizing Work Orders
Apr 12, 2023
4 min read
Work orders are a major part of fleet management and maintenance, but what should the ideal work order look like?
What is a work order?
Work orders are documents that allow you to track work performed on your vehicles, often used between fleets and third-party repair shops, or even with in-house shops. Work orders detail vehicle information, dates of service, descriptions of services performed, parts, labor and total cost of service.
Goal of work orders
Work orders are a great way to keep a consistent record of a vehicle’s service, as well as tracking the cost of each service for billing and accounting purposes. Work orders are often exchanged and approved to make sure fleets and shops are on the same page about work being done to a vehicle, which maintains accountability for both parties, as well as providing a good source for any warranty or insurance issues.
Types of work orders
There are a lot of different kinds of work orders out there, but when it comes to fleets, there are two relatively universal work order types you’ll see come across your desk:
-
Maintenance Work Order: These work orders are for routine maintenance tasks found in processes like inspections, repairs and preventive maintenance. They usually detail the maintenance task, vehicle service, required inventory and time and cost estimates.
-
Repair Work Order: Repair work orders are designed for unexpected repairs that crop up on the job. It outlines the problem that occurred, diagnostics for what work will need to be done, and estimates for time and cost.
What to include in your work order
Work orders need to be clear and easy to understand, so there’s a few things you’ll need to make sure you include in your work order:
-
Vehicle Information: Be sure to include make, model, and VIN.
-
Description of Work: The service should be very detailed and specific and should also include parts and inventory needed.
-
Timeframe: Deadlines and due dates should be assessed, as well as an hourly breakdown of how long service should take.
-
Labor and Material Costs: Labor and materials cost money, and that should be included in your work orders for cost transparency.
-
Payment Terms: Making sure there are clear details about how and when a vendor gets paid for services is vital in a work order.
-
Signature and Approval: Work orders are an agreement of service, so make it official and binding with signatures and approvals.
Pro-tip: Need somewhere to start? Give our free work order template a try!
How to create a good work order
-
Be Specific: The work order should clearly describe the task or project to be completed, including any necessary materials, tools, or equipment needed to complete the work.
-
Provide Detailed Instructions: The work order should provide clear and detailed instructions for completing the task, including any safety precautions that need to be taken.
-
Use Simple Language: Avoid using technical jargon or complex language that may be difficult for the person completing the work to understand.
-
Include Relevant Information: The work order should include all relevant information needed to complete the job, including customer information, equipment details, and any other relevant details.
-
Be Realistic: The work order should provide a realistic timeline for completing the work, taking into account any potential delays or challenges that may arise.
-
Provide a Clear Cost Estimate: The work order should provide a clear and detailed cost estimate, including labor and material costs, as well as any additional fees or charges that may apply.
-
Review and Revise: Before finalizing the work order, review it carefully to ensure that all necessary information has been included and that the instructions are clear and concise. Make any necessary revisions or updates as needed.
How to organize your work orders efficiently
-
Use a Digital System: Digital work orders are easily accessible, searchable, and can be updated in real-time.
-
Categorize by Priority: Identifying work orders by their priority level (urgent, high, medium, low) is a great way to allocate resources to tasks that matter most.
-
Sort by Due Date: Having a timeline of work to be completed can help you stay on tasks and manage your asset utilization in the meantime.
-
Create a Filing System: If you’re not organizing your work orders digitally, make sure you have an efficient filing system that lets you access work orders quickly, whether it’s by vehicle or by date.
-
Label Clearly: Develop a labeling system, whether physical or digital, that lets you easily identify different vehicles and services.
-
Automate Your Workflow: Automating work order processes is a great way to take the stress out of creating and organizing your work orders. Many fleet management software platforms will allow you to automatically generate work orders based on failed inspection items that immediately get sent to the shop.
Using work order software for your maintenance tasks
Managing your work orders in a fleet management software can help you automate many of the tasks you have to complete on a regular basis, including:
- Scheduling maintenance,
- Creating work orders,
- Prioritizing tasks,
- Tracking maintenance history,
- Reminding for upcoming maintenance,
- Monitoring performance,
- And analyzing data.
With an FMS like Fleetio, you can store your work orders digitally, so you never have to track down a paper trail again and always have your work order data right at your fingertips.
Want to get the most powerful insights from your fleet maintenance? Start your free trial in Fleetio or request a demo today.
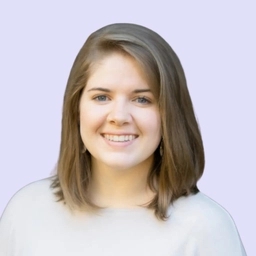
Senior Fleet Content Specialist
As a Senior Fleet Content Specialist at Fleetio, Peyton explores the voices and experiences that shape fleet operations. She focuses on how fleet professionals adopt technology, improve efficiency and lead their teams to bring clarity and context to the challenges happening across the industry.
View articles by Peyton PanikReady to get started?
Join thousands of satisfied customers using Fleetio
Questions? Call us at 1-800-975-5304