A Comparative Look at Equipment Tags
Jan 15, 2023
5 min read
Prior to the widespread adoption of smartphones and tablets, scanning barcodes to track their tools and small equipment wasn’t feasible for many small and midsize organizations.
Handheld terminals (i.e. portable computers with integrated scanners), while powerful and fully mobile, could cost thousands of dollars per unit. Conversely, while far more affordable, handheld barcode scanners needed to connect to a PC via a USB cable, effectively tethering personnel to their computer’s workstation. Due to these prohibitive costs and mobility restrictions, paper-based equipment tracking methods were often favored over digital approaches.
Fortunately, the emergence of smart devices (and subsequent rise of near-field communication (NFC) tags) have made digital equipment management far more accessible and agile. Thanks to their built-in cameras and NFC tag readers, smartphones and tablets can easily read barcodes, quick response (QR) codes and NFC tags to facilitate electronic check-in and check-out.
Types of tags for managing equipment
Now that many kinds of asset tags are viable for organizations of all sizes and industries, you might be wondering which technology best suits your equipment management needs. To answer that, we’ll be going over the advantages and disadvantages of barcodes, QR codes, and NFC tags in this blog post.
Barcodes
Laser-based barcodes, which first saw mainstream use in the 1970s, have stuck around for two primary reasons. First, they’re incredibly cheap to produce. Even for small organizations, the printing and material costs of producing barcode labels is virtually negligible. Secondly, there are countless free and easy-to-use barcode generators online. This means just about anyone can start creating their own barcodes in no time at all.
Unfortunately, barcodes aren’t without their drawbacks. Because they have to contain all of their information within a single row, a single barcode can only contain a small amount of information. For example, a barcode might provide a piece of equipment’s product number and storage location, but it likely won’t be able to provide supplementary details like the equipment’s condition, manufacturing date or equipment maintenance log. While this isn’t an issue when using equipment inventory software as additional information can be stored in a database (as opposed to on the barcode itself), it’s definitely something fleets should be aware of.
Furthermore, anyone who has used a grocery store self-checkout stand knows that scanning barcodes can be finicky. Barcodes require proper lighting and alignment to be read. Additionally, damage and debris can also render barcodes unreadable. While replacing a defective barcode with a fresh one isn’t particularly onerous, this downside can become a nuisance with certain kinds of equipment and tools.
QR codes
In many ways, QR codes are just better barcodes. Thanks to having an entire grid of rows and columns to work with, QR codes can contain far more information than barcodes. The dimensions of a QR code also provide them with greater resiliency to dirt and scratches. Even if a QR code is partially obscured, they can often still be successfully read. In addition, unlike barcodes, QR codes can be scanned from any direction, thereby making check-ins and check-outs faster and easier.
When it comes to QR code disadvantages, they share many of the same drawbacks as barcodes, but to lesser degrees. QR codes require ample ambient light in order to be read, so dark environments can lead to complications. Next, unlike the next technology we’ll cover, QR codes require line of sight between it and the device scanning it. While rotating a single asset to find its QR code label doesn’t take very long, over the course of several assets, this time can add up.
Streamline how you manage equipment
See how tags work with FleetioNFC tags
Near-field communication tags (also known as smart tags and info tags) are radio wave-receptive microchips attached to a copper coil usually contained within a sticker, label, or magnet. These incredibly small tags can be scanned by simply bringing a reader close to it with no specific alignment, line of sight, or ambient light required. Because of this, NFC tags are definitively the fastest equipment tag technology of the three.
And despite their size, NFC tags can also store far more data than even the most jam-packed QR code. Moreover, NFC tags are rewritable, meaning users can load new data onto their existing tags at no additional expense.
That last upside is particularly notable due to NFC tags’ primary drawback; compared to barcodes and QR codes, NFC tags are considerably more expensive. When purchased in bulk quantities, NFC tags generally cost around $0.20 per tag. Additionally, while upwards of 70% of modern smartphones possess built-in NFC readers, nearly a third do not. And while entry-level standalone NFC readers are rather affordable, they still tend to cost more than an equivalent barcode or QR code reader.
Managing equipment with software
And finally, any discussion of equipment tags would be incomplete without covering the software that complements them. Equipment management software enables fleets to track their tools and small equipment faster, easier and with greater accuracy.
With an equipment management system in place, all your personnel have to do to check-in or check-out an asset is to read its tag using their smart device. The fleet management app will instantly recognize the asset and log who it was assigned to and its geolocation. This automatic record enables managers to audit equipment usage, thereby promoting team accountability and reducing loss.
An additional benefit of equipment inventory software over paper-based management methods is that managers are able to monitor equipment usage in real-time. Managers can opt to receive instant notifications whenever a tag is scanned or an operator flags that an asset is in need of servicing. This level of immediacy helps ensure that critical equipment is repaired as soon as possible.
And speaking of repairs and equipment maintenance, equipment tags also streamline service work. Technicians can simply scan an asset’s tag to instantly pull up its service history. This makes identifying possible issues much easier and faster, allowing mechanics to spend less time digging through records and more time wrenching.
Whatever equipment tag technology you choose to use, the benefits they provide to fleets are numerous, especially when paired with construction equipment management software.
Leverage equipment tags to their fullest with Fleetio! Start a free trial or request a demo to see what our software can do for your organization.
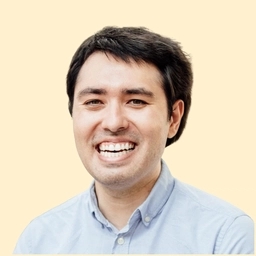
Fleet Content Specialist
Through interviews, blog posts and webinars, Alex covers the tactics and technologies exceptional fleet managers use to achieve results. By sharing their success stories, his work aims to inform and inspire fleet professionals of all stripes.
LinkedIn|View articles by Alex BorgReady to get started?
Join thousands of satisfied customers using Fleetio
Questions? Call us at 1-800-975-5304