Prioritize Asset Issues for Improved Maintenance
Prioritizing asset issues can help improve the health of your fleet, but it also provides a more efficient workflow process to get assets in and out of the shop quickly for increased uptime. Fleets can use fleet management software (FMS) to implement a structured process for issue prioritization and improved asset performance.
Jul 21, 2023
4 min read
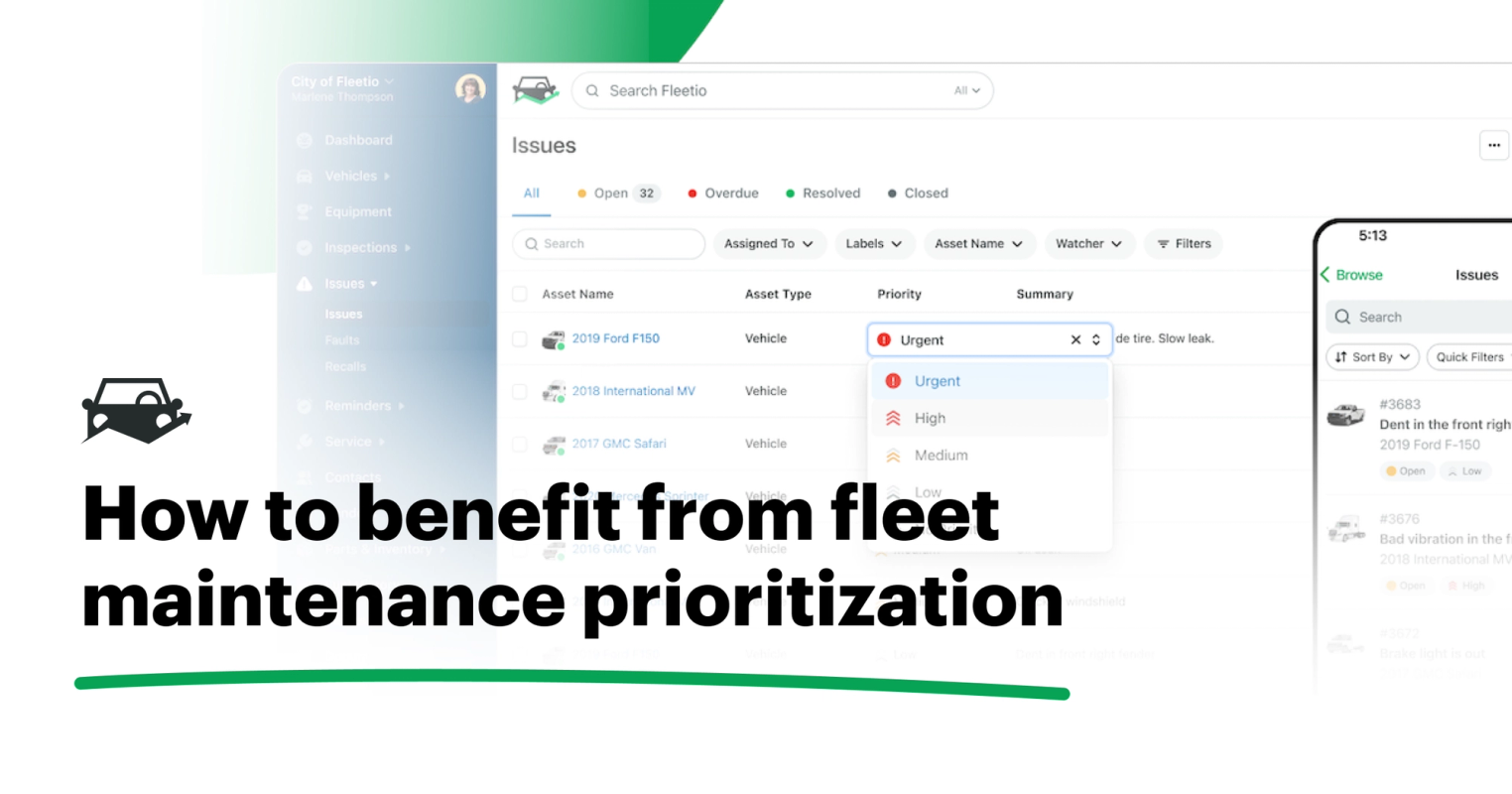
A Better Way to Juggle Asset Issues
In fleet, time is money — making operational efficiency integral to success. Adopting strategies to improve asset uptime can make a pretty significant difference in a business’s profitability. One such strategy is asset issue prioritization. Typically, preventive maintenance (PM) follows a routine schedule, but “surprise” asset maintenance issues arise on the road and in the field via fault code alerts, and they can even be noticed at start-of-day through pre-trip inspections.
Surfacing issues in real time makes vehicle issue management a little bit easier, but it can also be overwhelming to receive issue alerts, try to get the affected asset/s into the shop in a timely manner andstill respect technician availability when it comes to services that are scheduled. By reevaluating the conventional approach to maintenance schedules and shifting towards a prioritization mindset, fleets can reap numerous benefits, from cost savings to improved asset reliability.
Asset issue prioritization helps fleets move from reactive fleet management to proactive, allowing fleets to optimize their expenditure by focusing resources where they are needed most. By addressing critical maintenance needs of high-usage assets promptly, fleets can minimize costly breakdowns and avoid expensive repairs down the line. This proactive approach helps to reduce downtime, increase productivity and ultimately save money.
See how issue prioritization in Fleetio helps you focus your maintenance efforts
Benefits of Issue Prioritization
Neglecting maintenance needs can lead to unexpected breakdowns and reduced reliability, negatively impacting fleet operations. However, when fleets prioritize maintenance based on asset criticality, they can ensure that key vehicles receive timely maintenance and repairs. This issue prioritization approach enhances the overall reliability and useful life of assets, reducing the chances of unexpected failures and keeping operations running smoothly.
Fleets can leverage the power of data to effectively prioritize vehicle maintenance and asset issues. Using FMS, fleets can gather crucial insights into asset performance and downtime with digital work orders, service and inspection histories and compare those metrics to asset usage to better determine which assets should receive priority status. Analyzing this data enables fleets to make informed decisions on maintenance prioritization to proactively address issues before they escalate.
Furthermore, considering factors such as asset age, mileage, usage and historical maintenance patterns, fleets can develop customized plans that align with their specific needs and maximize the value derived from maintenance efforts.
Prioritize asset issues with ease in Fleetio!
Start free trialIssue Prioritization in Fleetio
Being reactive in maintenance and slow to respond to issues when they arise can really take the mobility out of an operation. By implementing clear priority terms, defining resolution expectations, regularly triaging issues, empowering your team to act and measuring performance, fleets can streamline their maintenance workflows and optimize fleet performance. Fleetio has implemented an issue prioritization feature to help fleets easily get ahead of major asset failures.
Common issue terms like critical, high, medium and low are widely used and easily understood in the fleet industry; however, it is essential to customize these terms to align with your fleet’s specific needs. By defining priority labels and descriptions in Fleetio, you can ensure that everyone on your team comprehends the significance of each priority level, facilitating better service planning.
Additionally, issue prioritization helps you collaborate with your team to establish realistic guidelines for issue resolution based on priority. By setting clear expectations, you can ensure that critical issues are promptly addressed, minimizing the impact on fleet operations. For example, critical issues may require resolution within 24 hours, while high priority issues may have a resolution timeframe of one to two business days. It is crucial to communicate these expectations to both drivers and technicians to foster a shared understanding of the importance of timely issue resolution.
Efficient prioritization relies on promptly assigning a priority to each issue that arises. Regularly triaging issues allows your team to assess the urgency and allocate resources accordingly. By sorting or filtering issues by priority, you can streamline workflows and ensure that critical tasks receive immediate attention. Utilizing issue prioritization in Fleetio can greatly assist in organizing and managing asset service effectively.
Because drivers are familiar with assets and run them daily, they play a vital role in identifying issues. Enabling them to assess and assign priorities when reporting issues can provide valuable insights into the severity and urgency of maintenance needs. By educating your drivers on how to evaluate and set priorities, you gain a deeper understanding of the impact on their productivity and can address issues more effectively.
When it comes to evaluating the effectiveness of your maintenance workflows, regularly tracking and analyzing issue resolution times against established priority resolution expectations plays a large role in success. By tracking these metrics and reviewing them in fleet reports, you gain valuable insights into your team’s performance and can more easily identify areas for improvement. This data-driven approach allows you to fine-tune your maintenance processes, optimize resource allocation and enhance overall fleet performance.
Ready to get your priorities in order? Start your free trial or schedule a personalized Fleetio demo today!
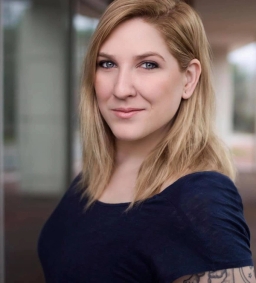
Senior Fleet Content Specialist
As a Senior Fleet Content Specialist at Fleetio, Rachael Plant uses her near decade of industry experience to craft practical content aimed at helping fleet professionals tackle everyday challenges with confidence.
LinkedIn|View articles by Rachael PlantReady to get started?
Join thousands of satisfied customers using Fleetio
Questions? Call us at 1-800-975-5304