Easing Technician Concerns Around Productivity Monitoring
No one likes the feeling of having someone constantly looking over their shoulder–especially fleet technicians. So, if you intend to start monitoring their productivity, it’s worth taking the time to assuage their concerns.
Mar 27, 2024
5 min read

When vehicles are an indispensable part of your operations, it's natural to want to maximize their uptime. In an effort to achieve that goal, many fleets track the productivity of their technicians to identify ways they can accelerate their maintenance and repair work.
But while this approach provides fleet managers with actionable insights regarding their service operations, technicians often feel uneasy about their pace of work being scrutinized. Worries over whether they're being "productive enough" can lead to anxiety, especially when matters beyond their control lead to work orders taking longer than expected to complete.
How to Address Mechanic Concerns around Labor Tracking
In an era where technicians are becoming increasingly hard to find, fleets should address these concerns head-on as part of a larger technician retention strategy. So, whether you're rolling out a new method of tracking technician output or onboarding technicians who aren't used to their performance being tracked, here's how you can assuage technician concerns about productivity monitoring.
Be transparent
Many of the concerns technicians have regarding productivity monitoring stem from uncertainty over what data is being collected about their performance and how that data will be used. By being transparent about both of these things, you can help your technicians feel more comfortable about their work rate being tracked.
Either as a group or one-on-one, show your technicians all of the data points you intend to capture and how that data is displayed via fleet reporting. This openness ensures your team is all on the same page about what criteria they're being evaluated on. And if you ever add any new maintenance KPIs to your productivity monitoring in the future, make sure to repeat this process to ensure no one is caught by surprise later down the road.
The second (and more challenging) part of being transparent is communicating how you intend to use the data that you capture to your technicians. If you plan on using metrics captured by productivity monitoring to inform decisions around raises or promotions, make that known. Critically though, if data will only be one of the contributing factors towards those decisions, stress that. Your technicians will probably feel a lot more comfortable about productivity monitoring once they know that their contributions to your organization won't solely be judged by numbers on a screen.
Finally, strive to develop a work environment where your technicians feel comfortable asking questions and voicing concerns about productivity monitoring (or anything else). Trust between technicians and fleet managers benefits all involved by reducing on the job stress and improving employee retention.
Improve your service workflow with labor hour tracking
Reward top performers
While productivity monitoring might primarily benefit fleet managers, the ability to measure technician performance on a granular level can also be used to reward personnel that go above and beyond. To prove that your organization values your technician's hard work, consider launching an incentive program based on technician productivity data. By awarding bonuses to top-performing technicians, you can highlight a positive aspect of productivity monitoring that your technicians might not have initially considered.
Fleet Manager Chuck Metoyer of Abt Electronics started a technician incentive program after bringing their fleet maintenance in-house. When we asked him to explain how it worked he said:
What we try to do is: If you do a good job, you get an additional amount inside your bonus. If you're a person that doesn't produce, you get less in your bonus. And you kind of use that number at the end of each quarter as a report card. And it kinda gets the guys to think: 'Well, I don't want to be the lowest guy in the bonus fund, plus I want to have some extra cash, so let me do a good job -- get the job done right.'
In Chuck's assessment, Abt's productivity-based quarterly bonus structure has helped the company turn around fleet assets more efficiently and effectively. By providing incentives that your personnel will want to strive for, it's possible a similar approach could have a similar effect on your operations.
Hear more lessons from fleet industry professionals
To create the ultimate fleet management resource, we interviewed more than a dozen fleet managers on how they address common operational challenges.
Download your free e-bookMake monitoring unintrusive
Beyond concerns around their performance being scrutinized, technicians can also be skeptical of productivity monitoring when it requires a change in workflow. If your personnel have settled into a groove, having them learn a new process in order to facilitate productivity monitoring can potentially result in friction.
So, to avoid that problem, fleets should ensure that whatever productivity monitoring method they roll out is unintrusive and user-friendly. After all, it wouldn't be fair to judge your technicians' productivity when they have to log their work into a system that actively detracts from their total wrench time.
With Fleetio, managing work orders and monitoring fleet productivity is simple and streamlined. During work order creation, you can enter a time estimate for how long you anticipate a task to take (based on historical data or your own intuition). Through this process, you can delegate work between your technicians more equally, which helps to prevent burnout.
Technicians can use Fleetio to report their progress on a work order in real time. And if they ever need to step out of the service bay for a moment, techs can clock in and out of tasks to maintain accurate labor hour counts. And once a task is done, fleet managers can view that work order to see if it was completed faster, slower or in line with expectations.
By addressing your technicians concerns about their productivity being tracked, you can accelerate your service operations while maintaining a positive work environment.
Discover why fleets choose Fleetio
Thousands of organizations across countless industries rely on Fleetio to manage their fleet activities. No matter the size of your fleet, Fleetio can help you track, analyze and improve your operations.
Learn more about Fleetio Go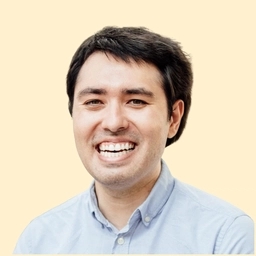
Fleet Content Specialist
Through interviews, blog posts and webinars, Alex covers the tactics and technologies exceptional fleet managers use to achieve results. By sharing their success stories, his work aims to inform and inspire fleet professionals of all stripes.
LinkedIn|View articles by Alex BorgReady to get started?
Join thousands of satisfied customers using Fleetio
Questions? Call us at 1-800-975-5304