Improving Service Workflows with Enhanced Service Tasks
The inability to link specific parts and expected labor hours directly to service tasks can hinder service workflows. With enhanced service tasks in Fleetio, fleets can better track and understand service costs — including expected vs actual labor hours — auto-assign parts to specific service tasks and improve technician and workload management.
Jan 30, 2024
4 min read

In a perfect world, the routine maintenance and repair activities that keep a fleet rolling would be seamless; however, the inability to link specific parts and expected labor hours directly to service tasks can hinder a smooth workflow.
Taking a manual approach with parts tracking on work orders can lead to incomplete or inaccurate data, even — and maybe especially — for routine services performed frequently. Plus, manual data entry is repetitive and time consuming. Similarly, lacking insight into the expected versus actual time a service task takes can lead to poor scheduling, uneven workloads, unnecessary downtime and, ultimately, fleet productivity loss.
Simplifying the Service Workflow
A comprehensive fleet maintenance system should help make your fleet’s service workflow as seamless as possible. That’s why Fleetio is introducing the addition of enhanced service tasks with parts and labor to its platform — to help businesses successfully reach fleet management goals.
For fleets handling maintenance in house, maintenance management consists of managing fleet technicians and technician productivity, workloads and schedules, parts inventories, not to mention putting out little fires all the while. By cutting down on task redundancies, automating more of the maintenance workflow process and gaining more in-depth information around service tasks, the job of maintenance management becomes a little more tame.
A Smooth, Seamless Service Workflow
Digital work orders in Fleetio are getting even better with the addition of enhanced service tasks with parts and labor!
Learn moreTechnician Productivity Insights for Optimized Labor Management
Sustainable workload division and scheduling for minimal downtime are major factors in keeping a service workflow moving efficiently. Knowing things like who excels at certain tasks and who takes a brunt of the workload can help fleets optimize service task assignments while getting a more accurate picture of service task times, allowing for improved service scheduling.
Fleets can use service histories or simply ballpark a baseline estimate for the length of time specific service tasks should take and set labor hour estimates accordingly. When service tasks with set labor expectations are added to work orders, technicians have clear visibility of expectations when logging entries against tasks. From there, fleets can compare expected labor hours against actuals for precise exception handling and enhanced operational efficiency.
Service Time Tracking
In Fleetio, technicians can clock in and out of jobs directly from digital work orders, allowing fleets to compare actual versus estimated service task times for improved scheduling, as well as insights into top performers and individual task proficiencies.
Auto-add Parts Associated with Specific Service Tasks
Inventory can already be a beast to keep up with, and having to manually add parts to work orders doesn’t exactly help. Whether you’re scanning a barcode, keying in a SKU or choosing from a drop down menu, you’re kind of wasting time unnecessarily, especially with routine or common maintenance tasks. If you have part numbers memorized, just know that may be an indication that you’re spending too much time on the wrong task.
Like labor hour estimates, fleets can link asset replacement parts to associated service tasks with the flexibility to create a part on the fly while adding linked parts. Linking parts to service tasks enables the automatic population of those parts on work orders because, let’s face it, ain’t nobody got time for that.
The Circle of (Inventory) Life
In Fleetio, fleets can link specific parts to associated service tasks, eliminating the need for repetitive data entry. Parts linked to service tasks are automatically added to work orders and inventory counts are adjusted accordingly. And by setting low stock or auto-reorder thresholds, you’ll sleep soundly knowing the parts you need will be where you need them — or at least somewhere in the stock room.
The Big Picture: Enhanced Service Tasks in Fleetio
Enhanced service tasks with parts and labor in Fleetio isn’t just about fixing a gap — although when the customers spoke, we listened — it’s about helping fleets improve their service workflow, saving valuable time and enhancing productivity.
By tracking technicians and analyzing expected versus actual labor hours, fleets can make informed decisions around task assignments and scheduling for minimal downtime. And by linking parts to service tasks, fleets can significantly cut down the time it takes to create a work order while adding another level of accuracy in inventory management. Both of these additions make it easier for fleets to track maintenance and repair costs and surface workflow inefficiencies.
Enhanced Service Tasks in Action
If seeing is believing, then you’ll probably want to see Fleetio’s enhanced service tasks with parts and labor in action. Schedule your personalized demo and become a believer.
Schedule demo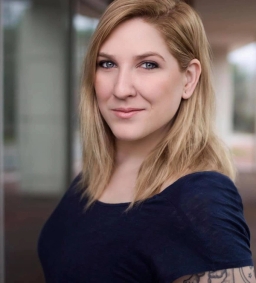
Senior Fleet Content Specialist
As a Senior Fleet Content Specialist at Fleetio, Rachael Plant uses her near decade of industry experience to craft practical content aimed at helping fleet professionals tackle everyday challenges with confidence.
LinkedIn|View articles by Rachael PlantReady to get started?
Join thousands of satisfied customers using Fleetio
Questions? Call us at 1-800-975-5304