A Guide to Heavy Equipment Maintenance Programs
Managing a fleet of heavy equipment requires specific care. The assets are expensive, the job site is rough and the fleet is often working miles away from a shop. Without a sound preventive maintenance program, you could be dealing with missed service, unexpected breakdowns and costly delays in your project.
Mar 28, 2025
8 min read
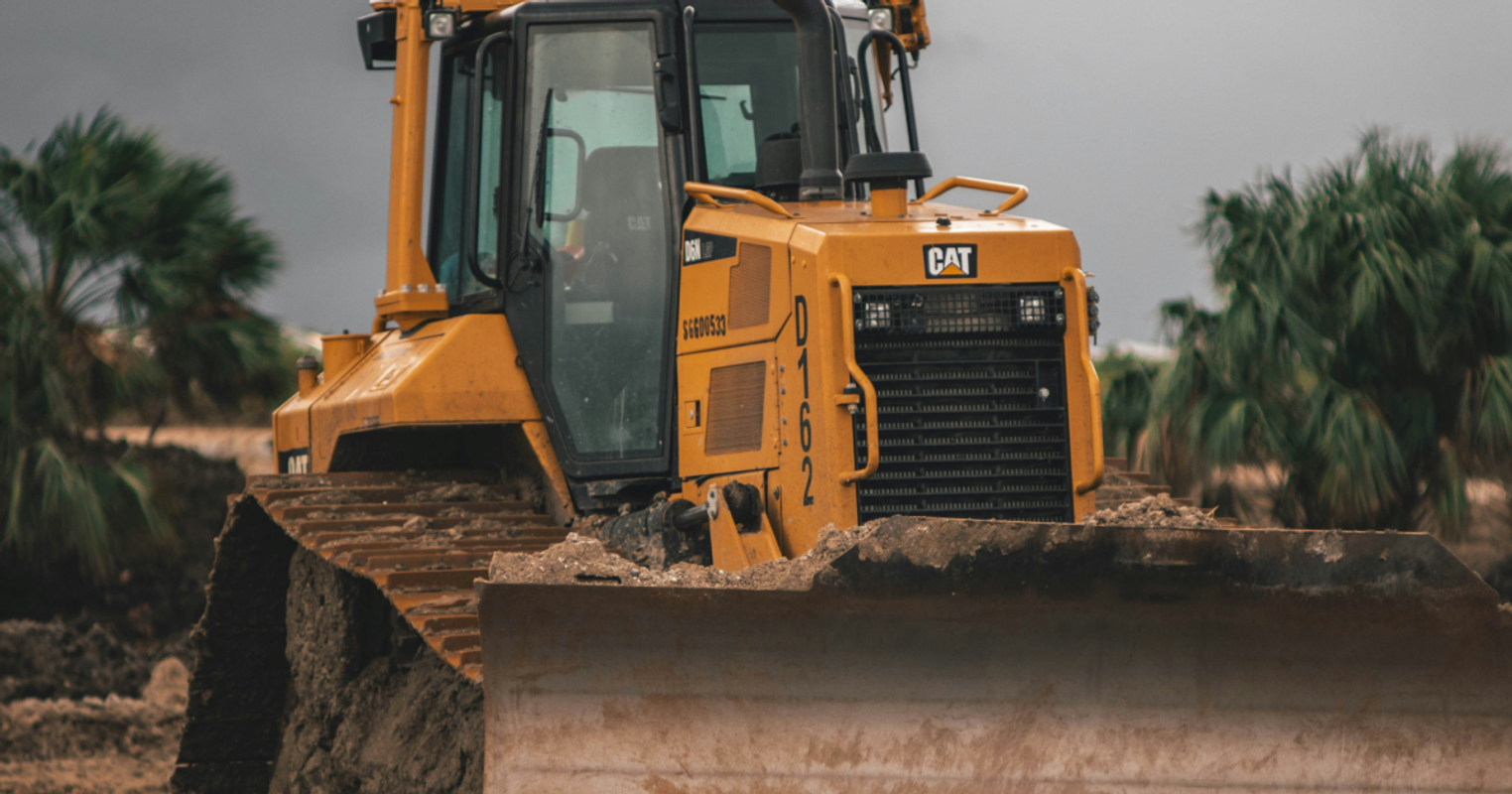
Developing an equipment preventive maintenance program is one of the best ways to regularly monitor heavy equipment conditions, maximize uptime and protect your investment in construction assets. Implementing a proactive equipment maintenance procedure means you'll get the most out of your investments by properly caring for them, whether they're tracked by engine hours or mileage.
Whether you’re managing heavy-duty construction equipment or smaller equipment and power tools for your landscaping or contracting business, you need a solution to avoid downtime on the jobsite. Adhering to an equipment preventive maintenance program helps you regularly monitor asset condition and make any necessary repairs.
Benefits of an equipment maintenance program
Having an equipment maintenance program is key to running a smooth operation if your business relies on equipment for your day-to-day work. The right equipment maintenance program can help you:
- Control heavy equipment operating costs
- Prioritize safety
- Improve equipment lifespan
- Increase employee satisfaction
- Reduce costly on-site breakdowns that can halt entire job sites
- Meet project deadlines by ensuring equipment is always operational when needed
- Maintain equipment resale value through documented maintenance history
4 types of equipment maintenance strategies
There are a few different approaches fleets can take to address equipment maintenance, but some have greater drawbacks than others. Here’s a quick breakdown of four of the most common strategies for equipment maintenance:
Preventive maintenance
Preventive maintenance can help guarantee that heavy equipment is serviced based on engine hours and usage cycles. Maintenance on heavy equipment like excavators and bulldozers is typically tracked by engine hours rather than mileage, following OEM recommendations or internal shop standards to maintain efficiency, but without automation, tracking usage manually can lead to overdue maintenance and unexpected failures.
Predictive maintenance
Predictive maintenance uses real-time telematics data to monitor asset health and trigger service before failures occur. It draws from the collection of data to determine if an issue is likely to occur so it can be intercepted before it impacts production.
This approach is particularly valuable for construction equipment where telematics from Caterpillar VisionLink and John Deere Operations Center can provide early warning of potential failures, automatically pulling fault codes, engine hours and sensor data to help maintenance teams act before issues escalate.
Condition-based maintenance
Condition-based maintenance is done as the need for it becomes obvious based on the overall condition of the vehicle and input like inspection reports. This approach still allows some lead time on potential breakdowns, but does not necessitate any maintenance that is not absolutely necessary.
Reactive repairs
Reactive repair maintenance is only completed in the event of an issue with the equipment. Equipment is not so much maintained as it is broken down and fixed.
Heavy-duty fleets require heavy-lifting maintenance
Keep your equipment running and your projects on track. Fleetio gives you real-time visibility into inspections, maintenance and asset health — whether they're parked on-site, in the yard or hard at work.
Dig deeperWhy choose a preventive maintenance program for equipment
For construction and heavy equipment fleets, preventive maintenance means fewer emergency repairs, lower costs and improved project timelines. By integrating equipment telematics data with Fleetio, fleet managers can automate maintenance tracking, reducing the risk of unexpected downtime.
Preventive maintenance allows you to:
- Be proactive to avoid breakdowns
- Limit unplanned downtime with scheduled maintenance
- Adhere to OEM guidelines for best operating practices
- Ensure the lifespan of the equipment
- Maintain eligibility for warranty
- Minimize the high costs associated with transporting heavy equipment for emergency repairs
- Ensure field technicians have all maintenance history available when servicing equipment on job sites
- Coordinate maintenance during low-utilization periods to prevent project delays
4 best practices for your equipment maintenance program
No matter what type of equipment you’re managing, keeping up with preventive maintenance can be difficult without an effective plan. Messy calendars, whiteboards and software solutions without real-time notifications can cause maintenance tasks to slip through the cracks and result in equipment breakdowns. By implementing these four best practices, you can reduce equipment downtime and improve the profitability of your fleet operation.
Automate equipment maintenance reminders
Tracking equipment usage allows you to know when preventive maintenance tasks are due, but manually tracking manually tracking usage for a dozen or more assets can be quite a headache.
Equipment management software automates the way you track equipment usage, making it easy to determine when maintenance tasks are due. Managers can create service schedules for individual pieces of equipment or manage schedules in bulk for similar types of equipment.
Once schedules are set, service reminders can be triggered by usage. With Fleetio, you can automatically sync engine hours from OEM telematics systems like Caterpillar VisionLink and John Deere Operations Center to trigger service reminders based on actual equipment usage rather than manual inputs. Managers receive reminders based on due soon thresholds. With advanced notification, managers have ample time to schedule maintenance when equipment isn’t being used to avoid downtime during work hours.
For heavy-duty equipment like in construction fleet management, fleet managers can pair their GPS and telematics system with equipment management software to automate service reminders. Odometers are updated automatically each day to trigger maintenance reminders.
Create work orders based on equipment inspection results
Equipment issues are often uncovered during routine fleet inspections. While identifying a new potential issue isn't preventive by nature, having the measures in place and following a set program will ensure a proactive process to prevent further escalation.
Inspections are critical for heavy equipment maintenance, especially when equipment is serviced on site and field technicians need comprehensive information about past repairs and current issues. Without a centralized system, issues can go unnoticed. With digital inspection workflows, you can automatically generate work orders when a fault is detected, ensuring repairs are scheduled before equipment failure occurs.
Effective equipment maintenance solutions streamline maintenance workflows and allow you to follow issues from identification to resolution. Managers can create work orders based on inspection item failures. Using software, you can assign digital work orders and track progress to ensure maintenance is completed promptly to increase uptime.
Collaborate with your team to expedite maintenance
Maintaining productivity is critical to your success. An equipment preventive maintenance program that enables team collaboration maximizes maintenance efficiency to keep your team productive on the jobsite.
Playing phone tag with technicians to understand maintenance needs and monitor service progress slows down operations and takes you away from other important tasks. Streamlining communication with a collaborative equipment management solution ensures you and your team stay on the same page regarding equipment maintenance.
Using a software and mobile app to connect with your team bridges the gap between field and office. Managers can assign mobile work orders, comment on line items and track maintenance progress and expenses.
Technicians can easily view work orders on a mobile app and collaborate with managers on repairs. Communicating in real time keeps your entire team in sync and allows you to ensure tasks are being completed correctly and on time.
An organized equipment preventive maintenance program allows managers to track every aspect of equipment maintenance remotely. Managers can get a high-level view of open and completed work orders, user comments, part usage and repair expenses in their configurable dashboard. Having all equipment data in one place allows managers to easily dive into granular details and quickly access the data they need.
Analyze service history to predict future maintenance needs
While automating service reminders and streamlining maintenance workflows is immensely valuable, analyzing past service is equally important in your quest to maximize equipment lifespan.
Managing your assets in an equipment preventive maintenance program provides a complete view of equipment details and past maintenance needs. With a comprehensive view of equipment service history, managers can monitor equipment health, take steps to increase asset lifespan and spot overarching trends across equipment.
Automatically recording service history ensures you have all the information you need when performing preventive maintenance tasks. By analyzing detailed service history, you can make data-driven maintenance decisions that positively impact equipment lifespan.
Establishing a strong maintenance program for equipment
No matter what type of equipment you're managing, keeping up with preventive maintenance can be difficult without an effective plan. Messy calendars, whiteboards and software solutions without real-time notifications can cause maintenance tasks to slip through the cracks and result in equipment breakdowns.
Wouldn't it be easier to keep up with equipment maintenance if you were reminded of tasks automatically?
With Fleetio's equipment preventive maintenance software, you can manage both over-the-road assets and heavy-duty off-highway equipment in a single platform, ensuring your entire mixed fleet is job-ready and properly maintained. Create service schedules for all of your equipment and automate service reminders based on actual usage data. With our mobile-first solution, you're notified of upcoming tasks and can collaborate with your team to efficiently complete preventive maintenance tasks, whether in the shop or at remote job sites.
If it ain't broke, fix it — before it is
Missed inspections cause breakdowns and breakdowns cause delays. But with the right tools, you can prevent it all. See why Fleetio is right for your fleet in just a quick walkthrough.
Let's talk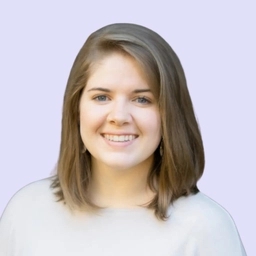
Senior Fleet Content Specialist
As a Senior Fleet Content Specialist at Fleetio, Peyton explores the voices and experiences that shape fleet operations. She focuses on how fleet professionals adopt technology, improve efficiency and lead their teams to bring clarity and context to the challenges happening across the industry.
View articles by Peyton PanikReady to get started?
Join thousands of satisfied customers using Fleetio
Questions? Call us at 1-800-975-5304