What You Can Learn from Breakdowns in Your Fleet
While every fleet aims to minimize vehicle breakdowns, few approach the problem from a data-driven perspective. By analyzing their breakdown data for trends, fleets can discover issues that might otherwise go unnoticed.
Mar 16, 2023
4 min read
It goes without saying that vehicle breakdowns are one of the biggest thorns in any fleet’s side. They grind productivity to a halt, seem to happen at the most inconvenient times and can blindside organizations with exorbitant fleet repair costs. For all those reasons, it’s understandable that most fleets would prefer to focus their attention on making up for lost time instead of ruminating on a major source of stress.
But the fact that breakdowns are so disruptive is precisely why fleets should take the time to take a closer look. By analyzing the data surrounding their vehicle failures, fleets can identify potential causes and develop effective countermeasures, preventing future breakdowns in the process.
To help fleets get started, we’ll be covering what kind of information fleets should record regarding breakdowns, what factors fleets should keep their eyes peeled for when examining their breakdown data and how fleets can best leverage any insights they glean.
But first, let’s quickly dive into how much vehicle failures cost fleets.
What is the potential cost of a vehicle breakdown?
While many factors influence how much a trip to the repair shop will set you back, some statistics from CarMD and AAA illustrate that the most common mechanical failures often cost a substantial sum to fix.
According to their research from 2021:
- The average check engine light repair costed around $400
- Brake pad replacements averaged about $200 per axle, but could easily cost double if there were hydraulic, rotor or drum problems
- Fuel pump replacements were typically priced around $500
- Catalytic converter replacements (the most common check engine light repair) were close to $1,350 on average
- And transmission system replacements easily ran into the thousands of dollars
It’s worth noting that inflation and part shortages have undoubtedly increased the cost of these repairs since these statistics were taken.
Now that the importance of preventing breakdowns has been well-established, let’s explore how fleets should prepare their breakdown data.
How to prepare your breakdown data for analysis
Before any fleet can start to learn from its breakdown, it’s imperative that they get their data in order. By taking the time to verify that their data is accurate, comprehensive and well-organized, fleets can ensure that any insights they uncover are derived from reliable intelligence.
1. Gather your vehicle-related records
Compile the make, model, mileage and service histories for all of their vehicles that have suffered a significant breakdown. These basic details will provide the groundwork for later analysis.
2. Add any breakdown-relevant information
Next, fleets should aim to add as much contextual detail as they can to each breakdown record. Notes on what circumstances the breakdown occurred under, who was operating the vehicle at the time of the breakdown, telematics readings and the like are all immensely valuable.
3. Assemble all your data into a single source of truth
Finally, fleets need to centralize all the breakdown-related information they have into a single source of truth, generally in the form of a spreadsheet or database. The easier this single source of truth is to read and interact with, the easier the subsequent analysis will be.
Notably, fleets leveraging fleet management systems (FMSs) don’t have to bother with most of these data preparations because the software they use takes care of things for them. Instead, they can simply pull up a fleet management report to instantly view whatever maintenance KPI they’re curious about. Calculating TCO is also much faster and easier with the help of an FMS.
On the lookout for statistical trends
To efficiently pore over large datasets, researchers keep their eyes peeled for patterns that constantly appear across whatever they’re examining. Fleets can adopt a similar strategy when scrutinizing their breakdown data.
Over a long enough period of time, it’s easy to dismiss commonalities between vehicle breakdowns as being merely coincidental. But when fleets take a close look at their data, they often uncover trends that would have otherwise gone unnoticed. Whether it’s a specific model of vehicle repeatedly suffering mechanical failures or a particular issue that keeps popping up across an entire fleet, trends can take on many forms and often differ between organizations.
The reason spotting trends is so useful is because they are often indicative of systemic ways organizations can improve their approach to fleet vehicle maintenance, efficiency and bottom line. If a specific factor contributes to 20% of a fleet’s vehicle breakdowns, eliminating that factor would result in massive savings and a significant improvement in safety.
Turning insights into action
Finally, once a fleet has thoroughly examined its breakdown data and identified matters worth addressing, they need to act on the insights they’ve gained.
For example, let’s say that a fleet observed that a certain model of vehicle they owned tended to falter after 75,000 miles. To get ahead of significant mechanical failures later down the road, that organization could modify its fleet maintenance schedule to pay extra attention to those vehicles as they near that threshold.
Fleets can also leverage insights gleaned from breakdown data to make more informed part purchases. Once a fleet discovers that a particular part that they have been using is failing faster than average, they can switch to a different brand (and justify any additional cost).
Breakdown insights can even be used to improve how personnel are trained. If a close inspection of telematics data reveals that rampant idling contributed to unnecessary wear and tear to a fleet’s vehicles, that organization can adjust its training procedures accordingly.
Analyze your operational data like never before
Make your data work for you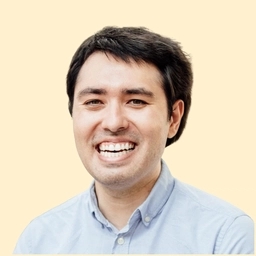
Fleet Content Specialist
Through interviews, blog posts and webinars, Alex covers the tactics and technologies exceptional fleet managers use to achieve results. By sharing their success stories, his work aims to inform and inspire fleet professionals of all stripes.
LinkedIn|View articles by Alex BorgReady to get started?
Join thousands of satisfied customers using Fleetio
Questions? Call us at 1-800-975-5304