Mastering Maintenance Inventory Management: Tips and Metrics
Reliably having a well-stocked supply of parts on hand is an essential part of performing in-house maintenance. By following proven best practices and keeping a close eye on specific metrics, fleets can optimize how their inventories are managed and restocked.
Nov 20, 2024
9 min read
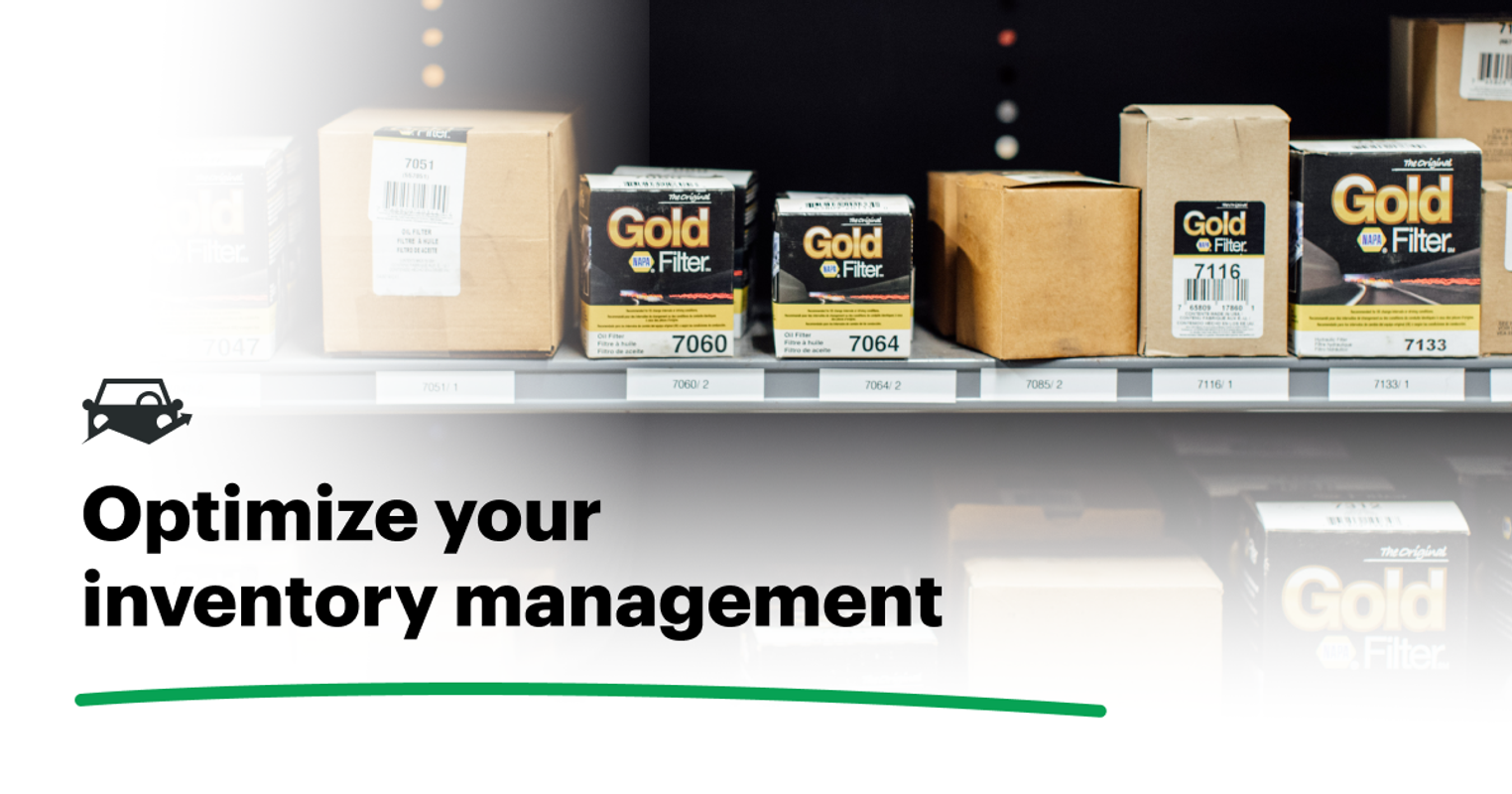
Even the smallest fleets that maintain their vehicles and equipment in-house go through a considerable amount of parts, consumables and supplies to keep their assets in action. In fact, parts represent about a third of vehicle maintenance costs for the average fleet. To ensure that your technicians always have the items they need on hand and that your maintenance budget is well spent, it’s critical that you monitor and re-stock your reserves mindfully through maintenance inventory management.
What is maintenance inventory management
By analyzing how your organization has historically gone through maintenance-related items, you can identify patterns that can inform your procurement strategy moving forward. For instance, if you observe that your fleet installs windshield wiper blades at a first rate during winter, you can get ahead of that need by stocking replacement blades when it’s still warm. This approach of purchasing parts in anticipation of future need is called proactive maintenance inventory management.
By being proactive with how they manage and restock their inventories, fleets are able to stockouts that can leave assets out of commission for extended periods of time. This thinking ahead distinguishes proactive equipment inventory management to reactive inventory management. With a reactive approach, organizations only restock when their reserves of a particular item reach a designated threshold. While not ineffective on its face, this reactivity can run into problems when unexpected surges occur and can leave organizations without critical parts on hand.
Tips to improve maintenance inventory management
If you’re looking to enhance the way your organization procures parts or keeps track of its inventory-related expenses, try out some of these proven best practices.
- Leverage inventory management software to track stock levels automatically and to record part information for improved organization
- Develop standardized storage procedures and reinforce those methods when training personnel
- Regularly audit your inventory levels to ensure maintenance needs are being met
- Review historical part utilization to stockpile high-demand parts and minimize overspending on rarely needed SKUs
- Establish relationships with preferred part vendors
Manage all aspects of your inventory
With Fleetio, organizations can track their parts, compare vendor prices and keep a close eye on costs all on a single platform.
Learn more4 Metrics to improve maintenance inventory management
1. Total Inventory Value
Because parts constantly fluctuate in value, it’s often tricky for fleets to manually estimate the total worth of the components they have on hand. This complexity can make insightful metrics like total cost of ownership more difficult to calculate accurately. Fortunately, the Last-In First-Out (LIFO) and First-In First-Out (FIFO) inventory valuation methods can help organizations get their accounting in order.
Last-In First-Out refers to the assumption that the last part to be added to an inventory is the first to be used. First-In First-Out assumes the opposite, that the first part to enter an inventory will also be the first to be used.
While virtually exclusive to the US, LIFO is especially effective when part price inflation is anticipated to last for long periods of time. By counting their part costs at their highest, organizations are able to reduce their profit margins and, in turn, lower their taxable income. That being said, it’s worth noting that organizations are required to file that they’re using the LIFO method when reporting to the IRS. FIFO is far more common than LIFO, especially around the world. While less advantageous when it comes to taxes, FIFO offers a more precise view into a fleet’s costs.
2. Part Utilization
While fleet personnel often have a hunch when it comes to which parts they use the most, actually running the numbers around part utilization can often be eye-opening. By identifying their most commonly used parts (and what vehicles they’re being used with), fleets can better understand the needs of their assets and account for future part demand by procuring more strategically.
For example, if a fleet finds that they go through a surprising amount of air filters, it might be in their interest to stock up on air filters if they go on sale. Alternatively, they might consider looking into alternative air filter brands that could offer greater longevity. It might even be worth changing equipment maintenance procedures to address air filter issues at an earlier stage or on a more frequent basis.
3. Stockout Rate
Having parts on hand when you need them is the whole point of keeping a maintenance inventory. So when something needs replacing but your technicians don't have immediate access to the part they need, that failure is worth noting. Such incidents are referred to as "stockouts" and a fleet's "stockout rate" expresses how often that problem occurs as a percentage.
How to Calculate Stockout Rate
Stockout rate (%) = (number of stockouts/total number of inventory requests) x 100
By calculating this metric, you'll be able to determine how often your technicians were left empty-handed after searching your shelves. To minimize downtime due to waiting for parts to arrive, you should strive to lower your organization's stockout rate as much as possible.
4. Inactive Stock Percentage
To optimally stock a parts reserve, fleets have to strike a fine balance between being prepared for any scenario and not purchasing more than they need. While it's obviously good to have any part an asset might need within reach at all times, excessive part purchasing incurs expense with no meaningful gain. Fortunately, fleets can calculate their inactive stock percentage to help guide their procurement strategy.
How to Calculate Inactive Stock Percentage
Inactive stock (%) = number of inactive inventory items/total number of inventory items
In the formula above, an inactive item is defined as a SKU that hasn't been requested during the time period the metric applies. For example, if you're looking to calculate your inactive stock percentage over the last year, you would need to identify how many of your SKUs saw no use over the last 12 months.
Other maintenance inventory best practices
In addition to keeping a close eye on key metrics, fleets can improve their inventory management approach by following these best practices:
1. Anticipate part needs of high-mileage vehicles
While it’s possible for any part to fail at any time, many components are expected to last well into a vehicle’s lifespan. Alternators are a classic example of this as, in most cases, they tend to function without issue for around 100,000 miles. Past that point, however, alternators are known to commonly need repairs or replacing. Because these kinds of parts don’t require replacing as often as other parts, fleets often don’t keep them on hand.
To maximize uptime, fleets with high-mileage vehicles should identify the kinds of parts their most seasoned assets will likely require (based on their mileage). By always having those parts on hand, fleets can quickly return high-mileage vehicles to the field after they experience an anticipated issue.
2. Track active part warranties
It goes without saying that fleets can significantly reduce their maintenance expenses by taking advantage of warranties when their vehicles or equipment need servicing. But despite how much money warranties can save organizations, it’s not uncommon for them to go unclaimed. It’s up to fleets to keep track of part warranties available to them, and without a dedicated system in place, many organizations often don’t realize that they could be receiving replacement parts at little to no cost.
To ensure such opportunities never pass them by, fleets should employ some means of logging which of their parts are under warranty. This can be accomplished with paper documents, spreadsheets or inventory management software. Whenever a part fails, fleet personnel can check their records to see if that particular part has an active warranty or not. Of course, this approach only works if warranty details are accurate and up to date, so whether you’re working with an inventory spreadsheet or specialized software, make sure to audit your records on occasion to ensure data quality.
For Fleetio Users
Add warranty information to individual parts and receive a notification when a repair is being performed on a part that is still covered under warranty. Set warranty alerts based on purchase date or install date.
3. Keep things organized
In much the same way that it’s easier to locate things at a neatly organized retail store than at a randomly arranged flea market, clear organizational practices make sorting through parts inventories far more manageable. Even the smallest inventories benefit from grouping related items together and dedicated shelves to specific kinds and categorizes of parts.
The advantages of systematic organization are especially apparent when you consider how many fleets reserve a shelf solely for part cores. Because part cores can be returned to their manufacturers in exchange for a rebate, it’s in any fleet’s best interest to never lose track of them. By having a designated space just for part cores, it couldn’t be easier for fleet personnel to locate and ship them out. And by removing as many obstacles to the part return process as possible, fleets get to reap the rewards of part core rebates far more consistently.
The role of inventory management software
While all of the metrics highlighted in this blog post can help fleet professionals manage their maintenance inventories more effectively, taking the time to calculate them can be quite time-consuming. Fortunately, with a computerized maintenance management system (CMMS), you can access these and other metrics anytime you want without ever having to pick up a calculator or update a spreadsheet. Reporting and analytics tools offered by inventory management systems help you better understand the state of your maintenance inventory, how your resources are being spent and what you might want to do to further optimize your operations.
Fleetio takes things a step further by acting as another pair of eyes for fleet professionals. For instance, when an item runs low, Fleetio can automatically notify specified users, prompting them to reorder before it’s too late. Additionally, Fleetio allows users to compare vendor prices when shopping for parts, ensuring they get a good deal, even when they don’t have time to visit vendor websites individually. By always keeping you in the know, Fleetio helps organizations rightsize their inventory to reduce unnecessary costs while still being prepared for whatever their fleet may require.
Discover why fleets choose Fleetio
Thousands of organizations across countless industries rely on Fleetio to manage their fleet activities. No matter the size of your fleet, Fleetio can help you track, analyze and improve your operations.
Book a demo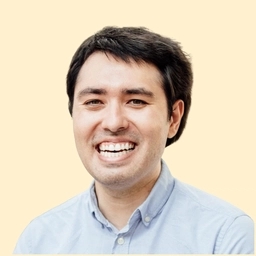
Fleet Content Specialist
Through interviews, blog posts and webinars, Alex covers the tactics and technologies exceptional fleet managers use to achieve results. By sharing their success stories, his work aims to inform and inspire fleet professionals of all stripes.
LinkedIn|View articles by Alex BorgReady to get started?
Join thousands of satisfied customers using Fleetio
Questions? Call us at 1-800-975-5304