Improving Preventive Maintenance with Work Order Calendars
A well-structured preventive maintenance (PM) program helps improve fleet assets’ useful life, safety and overall return on investment (ROI) by significantly reducing the risk of unexpected breakdowns and minimizing downtime. One of the most effective tools to support and improve PM programs? The work order calendar.
Aug 21, 2024
5 min read
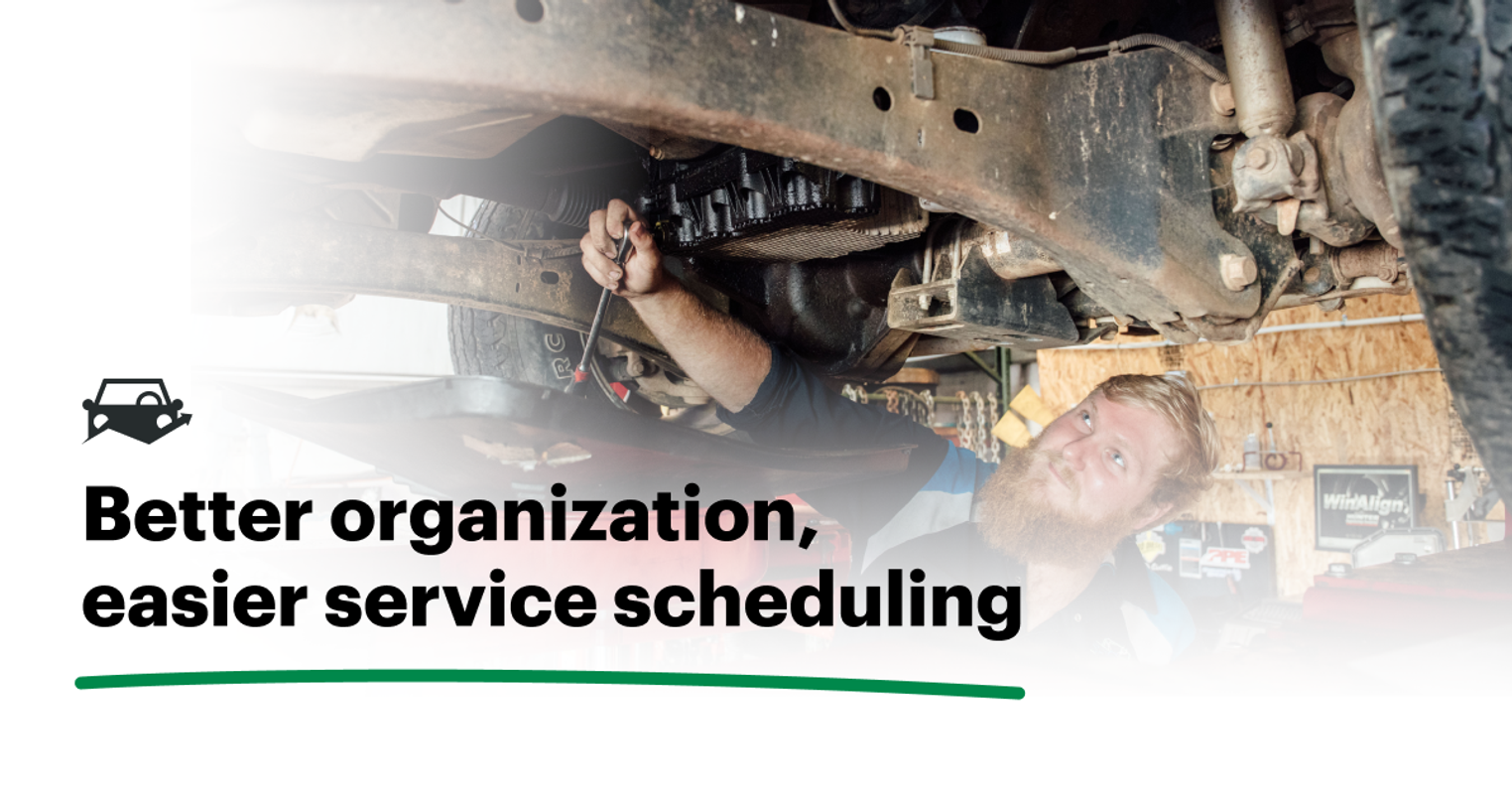
PM can be a fickle mistress, but that doesn’t mean it has to be. Managing maintenance and repairs becomes a lot easier when you can see what’s scheduled, what’s coming up due, what the repair priority is and which technician is assigned to what work order. Having an easy-to-read visualization of this information — in the form of a work order calendar — provides a high level overview that you can take a deeper look into for more specific service data. But before we get into the nitty-gritty of work order calendars, let’s take a look at establishing a fleet preventive maintenance program that best meets your assets’ needs.
Explore Work Orders in Fleetio
A PM Program Framework Just for You
Many fleets build their PM programs around OEM specs, which already provides a strong foundation. These specs, however, don’t necessarily take into consideration the environment in which an asset operates, and some environments are rougher than others. Understanding how daily operations affect specific assets can help you determine if — and what — additional PM tasks may be needed to keep them safe and productive. Asset usage, age and wear and tear patterns can all impact PM needs. High-usage vehicles or those that perform in harsh conditions, for instance, may need more frequent inspections, tailored maintenance tasks and high-durability replacement parts.
For Fleetio Users
Track recurring component issues via digital inspections and unscheduled downtime histories by asset to see if parts durability may be an issue, or if there is an underlying component issue that’s been overlooked.
Once you surface the “problem children” in your fleet, you can better determine the optimal maintenance intervals for each based on a combination of OEM recommendations, historical performance, inspection and service data, as well as current usage and operational demands. If you’re not already using a preventive maintenance program software or fleet optimization platform — like Fleetio — you can always use a comprehensive maintenance spreadsheet to help track the particulars.
While manually tracking service data is definitely tried and occasionally true, using fleet maintenance and management technologies provides the added benefit of improved maintenance compliance, faster service times and reduced breakdowns through in-depth work order management. They also allow you to fine-tune your PM programs based on both direct and indirect maintenance data.
Direct data, including work orders, service histories, inspections and PM schedules, provides insight into the specific maintenance activities performed on each asset and surfaces on-time and overdue services. Indirect data, including fuel consumption, idle time and diagnostic trouble codes (DTCs) offers supplementary information that can help identify underlying issues that may be going unnoticed. Having the ability to easily analyze this data collectively can better inform you around decisions regarding adjusting PM checklist items, identifying potential problem areas and optimizing asset performance and productivity.
Looking to strengthen you PM processes?
Look no further! There’s no better place to start than applying the basics. Check out a few ways to take your PM program to the next level.
Learn moreImprove Your Preventive Maintenance Game
Alright, it’s time. Let’s talk about the work order calendar, what it can do for you and how it works in Fleetio.
The work order calendar — or, more officially, Fleetio’s Work Order Calendar View — makes it easier to spot service related information and manage service tasks, allowing you to quickly review the status of upcoming, ongoing, overdue and completed tasks, as well as monitor shop productivity. This real-time status tracking helps you keep a finger on the pulse of maintenance tasks, enabling you to address delays promptly and keep the fleet running smoothly.
Simply input a scheduled start date on work orders, and you’ll automatically be able to view scheduled services in a calendar view organized by week, month, vehicle and assignee. You can also easily track how often actual work order start dates align with scheduled start dates and compare actual start dates against completion dates to identify and remedy operational inefficiencies.
While the work order calendar view can greatly help improve workload balance in the shop, it also plays a significant role in time management — and who doesn’t like to get a little time back in their day. The calendar’s clear overview of scheduled maintenance helps you ensure that assets are serviced during non-peak hours, minimizing disruptions to daily operations and allowing you the flexibility to better prioritize critical services as they arise.
Let me introduce you…
...to my favorite Fleetio feature — the digital work order. Expediting service workflows? Check. Providing a clean calendar view? You bet. Improving on-time maintenance compliance? Oh, yeah.
Check it outDeveloping a strategic PM program based on the fleet’s needs and integrating it with work order calendars doesn’t just enhance the accessibility of your truck maintenance log, it helps streamline scheduling and improves your ability to tackle issues as they arise — whether that’s asset issues or process issues. The result? A more proactive approach to maintenance that not only can extend assets’ useful life but also improves cost control, reduces downtime and helps keep assets road ready.
PM scheduling you can count on
Keeping up with PM tasks can be difficult. Fleetio helps keep you up to speed with service reminders on both custom and standardized service intervals.
Learn more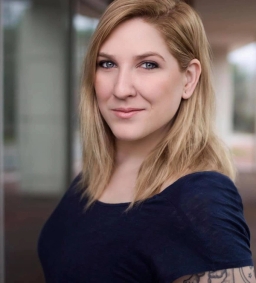
Senior Fleet Content Specialist
As a Senior Fleet Content Specialist at Fleetio, Rachael Plant uses her near decade of industry experience to craft practical content aimed at helping fleet professionals tackle everyday challenges with confidence.
LinkedIn|View articles by Rachael PlantReady to get started?
Join thousands of satisfied customers using Fleetio
Questions? Call us at 1-800-975-5304