How to Build a Fleet Preventive Maintenance Schedule
A preventive maintenance schedule is one of the most effective ways to reduce unplanned downtime, control costs and extend asset life. When you service fleet vehicles before issues arise, you keep operations running smoothly and avoid costly surprises.
May 12, 2025
17 min read
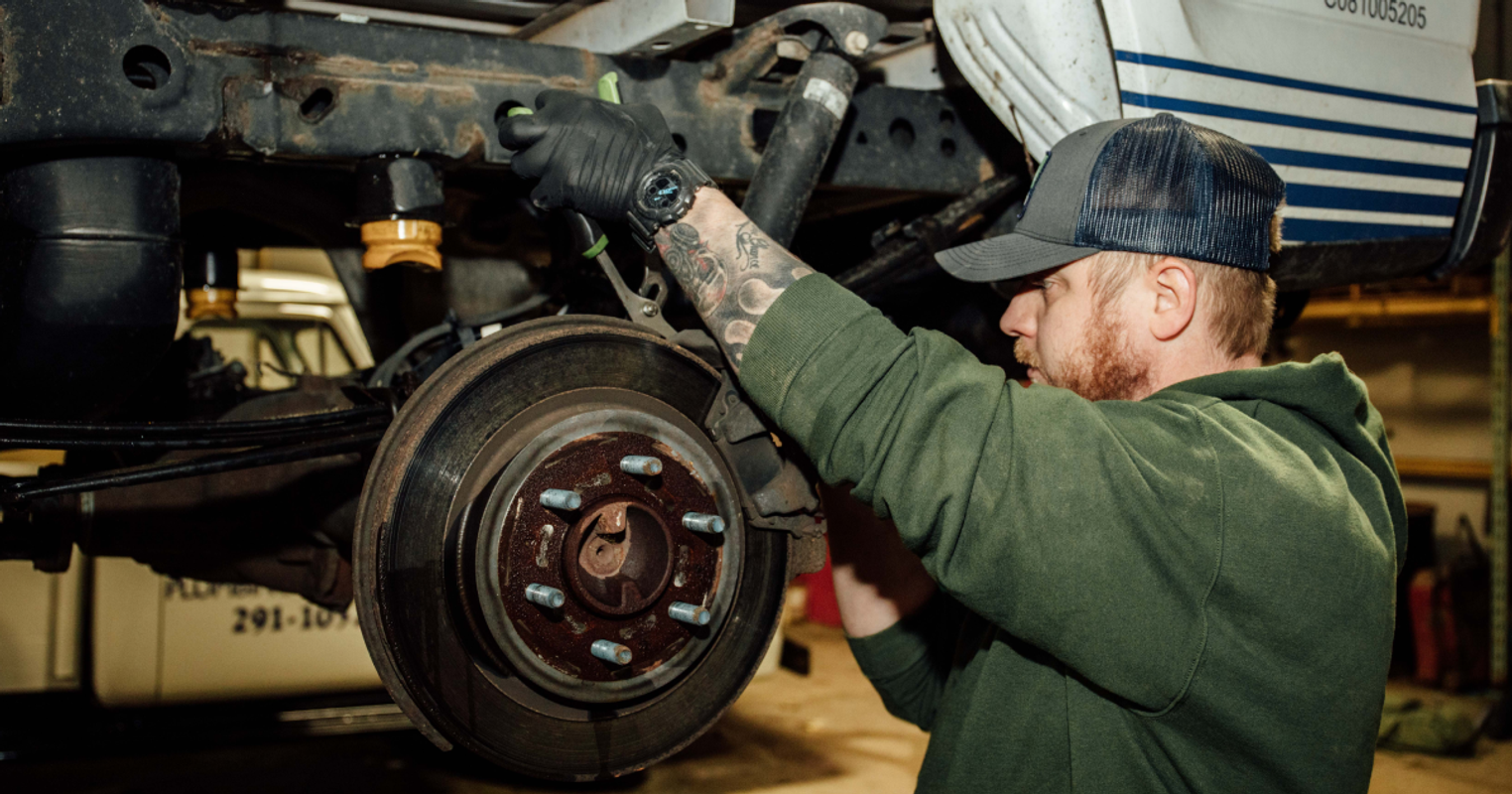
TL;DR: What is a fleet PM schedule?
A fleet preventive maintenance (PM) schedule is a structured plan to service vehicles before breakdowns occur. Using regular intervals based on time, mileage, or engine hours helps fleets reduce downtime, control costs, and extend vehicle life.
Steps to build an effective PM schedule:
- Inventory your assets: Record make, model, usage, and driver assignments
- Log service history: Centralize past maintenance to improve scheduling
- Follow OEM guidelines: Use manufacturer intervals as a starting point
- Create a service calendar: Plan and stagger tasks to avoid bottlenecks
- Track usage data: Use odometer or hour meter readings to trigger service
- Use maintenance software: Automate reminders, manage work orders, and track compliance
Fleet maintenance software improves consistency, prevents missed tasks, and provides data-driven insights to keep operations running smoothly.
Content Overview
Preventive maintenance (PM) is the practice of servicing fleet assets on a routine schedule to avoid unexpected breakdowns. A strong PM program helps reduce downtime, extend asset life and keep operating costs under control. In this guide, we’ll break down the types of maintenance, explain why scheduling matters, and show you how to build a custom PM schedule step by step.
Jump to a topic
What is a preventive maintenance schedule?
A preventive maintenance schedule is a structured calendar of recurring inspections, services and part replacements designed to prevent breakdowns, reduce downtime and extend the lifespan of fleet assets.
It acts as the execution layer of your maintenance strategy, detailing when each service task should occur, which asset it applies to, and who’s responsible for completing it.
This is different from a preventive maintenance plan, which defines the overall strategy: what tasks need to be done, on which assets and how often. The schedule brings that plan to life through timing, assignments and real-world execution.
Why preventive maintenance schedules matter
Creating a structured PM schedule is one of the most effective ways to reduce operating costs and improve fleet reliability. Benefits include:
- Fewer unplanned breakdowns and roadside emergencies
- Longer asset lifespan and improved resale value
- Better safety and compliance with regulations
- Clearer insight into future service needs
- Lower total cost of ownership (TCO) through data-driven decision-making
Types of preventive maintenance schedules
Preventive maintenance schedules can be structured in different ways depending on your fleet’s size, asset types and usage patterns. Most fleets use a combination of time- and meter-based scheduling, paired with a proactive maintenance strategy.
Time-based vs. meter-based scheduling
These are the two most common methods for setting maintenance intervals:
- Time-based: Service tasks are scheduled by the calendar (e.g., every 90 days)
- Meter-based: Intervals are based on usage, such as odometer readings or engine hours (e.g., every 5,000 miles or 300 hours)
Meter-based scheduling is often more accurate for fleets with variable asset usage.
Types of maintenance strategies
There are three primary approaches to maintenance in fleet operations:
- Corrective maintenance: Performed after a failure has occurred. This reactive approach can lead to costly breakdowns and unplanned downtime.
- Preventive maintenance (PM): Scheduled tasks – like inspections, fluid checks or filter replacements – designed to reduce the chance of failure. This guide focuses on PM as the most sustainable strategy.
- Predictive maintenance (PdM): Uses service history, diagnostic data, or telematics to forecast when an asset may need maintenance, allowing you to address issues before they arise.
Example of Predictive Maintenance
A fleet manager realizes that the alternator in most vehicles of a certain make and model dies between 100-115k miles. Rather than waiting to see if the trend holds true, they decide to replace the alternator on similar vehicles once they get close to 100k miles in order to avoid the costs of a vehicle breakdown away from the shop.
Are you managing maintenance — or is it managing you?
Fleet maintenance is more than just repairs and PMs — it’s about eliminating downtime and streamlining your entire workflow. This free guide, built with insights from industry pros, gives you proven strategies to take control of your maintenance program.
Put in your handsHow to Create a Preventive Maintenance Schedule (Step-by-Step)
A preventive maintenance program allows fleet managers to improve their overall uptime and reduce the costs associated with unplanned repairs, as well as extend the lifetime of the assets in their fleet. Here are a few components of a fleet PM program.
1. Inventory your fleet assets
A complete, accurate asset inventory is the foundation of any preventive maintenance (PM) schedule. Without knowing what you're servicing, you can't plan for consistent or cost-effective maintenance.
Start by creating a centralized asset list that includes all vehicles and equipment requiring regular maintenance. Include the following information for each asset:
- Year, make, model
- VIN, license plate, department/branch
- Assigned driver or team
- Asset class or type (e.g., light-duty truck, generator)
- Acquisition date or in-service date
Use a fleet management system to import and store this data, or build out an editable master spreadsheet if software isn’t in place yet.
Notes:
- For fleets with seasonal assets or equipment on lease, include operational windows and return dates in your inventory
- If your fleet includes mixed asset types (like vehicles and equipment), you may need to track slightly different data fields
- Assign a team member to maintain this list over time – it’s especially critical during purchasing or asset disposal
2. Document service history
A documented service history gives you insight into each asset’s past performance and helps you build a smarter PM schedule. It reduces guesswork, prevents duplicate work, and reveals trends that could indicate deeper issues.
Begin by collecting all existing maintenance records in a vehicle maintenance log (digital or paper) from shops, internal systems, and spreadsheets. Consolidate them into a single source of truth and attach them to each asset’s record in your fleet maintenance software. Include details like:
- Date of service
- Service type or system (e.g., brakes, electrical)
- Vendor or technician
- Odometer or hour reading at time of service
- Cost and parts used
For each entry, try to capture enough detail to inform future decisions. Look for patterns like repeat failures or high-cost systems to help prioritize PM tasks going forward.
Notes:
- If service history is incomplete, start fresh and commit to capturing clean data moving forward
- Don’t forget to include work done by third-party shops, not just in-house maintenance
- Tag entries consistently (e.g., “engine” or “suspension”) to make long-term reporting more useful
3. Define OEM maintenance intervals
OEM guidelines give you a baseline for what maintenance tasks should be performed and when. Starting with manufacturer recommendations ensures that your assets are maintained in line with safety, warranty and performance standards.
Just implementing my PM schedule [has] cut us down at least 20-30 percent of downed vehicles. Prior to me getting here, most of them were probably dropping dead at that 25-30,000 mile range, and now some of my UTVs are pushing onto 45-50,000 miles. So now, I’m looking at a completely different fleet replacement cycle, because I’m getting an extra 15-20,000 miles out of some of these UTVs. That’s, you know, that’s awesome. Kade Haney, Kualoa Ranch
Review the owner's manual or manufacturer resources for each asset to gather recommended service intervals based on mileage, engine hours or time (e.g., every 5,000 miles or 6 months). Capture the following:
- Recommended services (e.g., oil change, tire rotation, filter replacement)
- Suggested intervals (mileage, time or usage-based)
- Any warranty-related requirements
Document these recommendations in your fleet maintenance system so they can be used to automate service reminders and track compliance. From there, you can adjust frequencies based on real-world asset usage or environmental conditions.
Notes:
- Always begin with OEM guidance, but don’t treat it as one-size-fits-all – customize for asset type, age, climate and usage patterns
- Use a centralized source like Edmunds if original manuals aren’t available
- If your fleet includes upfitted or specialized equipment, note that OEM schedules may not cover all components (e.g., lifts, PTOs)
4. Create a service calendar
Once you’ve defined what maintenance needs to happen and how often, the next step is to create a calendar to manage when and where those tasks will occur. A preventive maintenance calendar helps you anticipate downtime and coordinate repairs without disrupting operations.
Start by mapping out maintenance intervals for each asset based on OEM guidance and actual usage patterns. Then, assign service dates using your maintenance scheduling software or a shared calendar system. Build in buffer time for scheduling delays and vendor coordination.
Consider staggering service dates for similar assets to avoid having multiple units out of commission at the same time.
- Set time-based and usage-based reminders (e.g., 90 days or 5,000 miles)
- Factor in shop capacity and technician availability
- Sync with inspections or registration renewals where possible
Notes:
- Digital calendars tied to odometer or hour meter readings provide more accuracy than static time-based reminders
- Use a color-coded calendar or dashboard view to easily visualize upcoming service needs across the fleet
- For assets with irregular usage, dynamic scheduling based on utilization data is more effective than fixed intervals
5. Track usage data to trigger PM
Preventive maintenance is most effective when it’s tied to how your assets are actually used – not just the calendar. Tracking usage data like odometer readings and engine hours allows you to trigger service tasks based on real-world wear and tear.
Log usage data regularly for each asset, either manually (via driver input) or automatically through telematics integrations. Feed this data into your fleet maintenance software to generate service reminders and performance insights.
Usage data helps ensure you’re servicing assets at the right time – neither too early (wasting resources) nor too late (risking downtime).
- Odometer readings for vehicles
- Hour meters for equipment
- Fuel consumption or GPS data as supporting metrics
Notes:
- Automate data collection where possible to reduce errors and save time – connect telematics or use a driver app for quick input
- For pooled or high-mileage assets, increase the frequency of usage monitoring to avoid missed service intervals
- Consider alerts for sudden spikes or drops in usage, which may indicate abnormal asset behavior
Comparing ways to track preventive maintenance schedules
There’s no one-size-fits-all approach to tracking preventive maintenance, but the right tool can make it easier to stay on top of upcoming service tasks and avoid missed intervals. Here’s how different methods compare:
Method | Overview | Best For | Limitations |
---|---|---|---|
Spreadsheet | Basic rows and columns for assets, tasks, intervals, and dates. | Small fleets just getting started with PM tracking. | Manual updates; limited automation or alerts. |
Checklist | A simple list of routine tasks, tracked on paper or digitally. | Technicians needing a task-by-task reference during service. | Doesn’t show timing or usage intervals; easy to lose track. |
Calendar | Paper or digital view of service due dates by day or month. | Visualizing time-based tasks across teams. | Doesn’t track mileage or usage-based needs. |
Gantt chart | Visual timeline showing overlapping service tasks by asset. | Managing complex PM schedules across multiple vehicles. | Requires manual setup and updates; can get cluttered. |
Fleet maintenance software | Dynamic, automated view of all PM tasks, tied to usage data. | Fleets needing real-time tracking, alerts, and historical reporting. | Requires setup and team adoption, but offers long-term ROI. |
Don’t let another maintenance task escape your grasp
When maintenance falls through the cracks, breakdowns follow. Fleetio helps you automate preventive schedules, maintain compliance and keep every vehicle on track, no matter how many you manage.
Get more on maintenancePreventive maintenance best practices
Implementing a fleet maintenance schedule is one thing; sticking to it is another. Many fleets still use paper work orders and spreadsheets to manage their PM, which can be inefficient and cause vehicles to miss routine maintenance, leading to downtime and costly repairs.
While you may have a planned preventative maintenance (PPM) schedule in place, check out these best practices to see how a fleet management system can help you increase efficiency.
1. Align PM schedules with real usage
Scheduled maintenance should reflect how your assets are actually being used. Usage-based service reminders—triggered by odometer or hour meter data—help ensure maintenance tasks are timely and relevant.
- Set up automated reminders based on actual mileage or runtime
- Use telematics or driver input to capture accurate usage data
- Avoid one-size-fits-all intervals across different asset types
Pro tip
Paper-based systems can introduce delays and inaccuracies. Digital tools like Fleetio improve data quality and reduce missed service events.
2. Use inspection results to detect early issues
Routine inspections can uncover issues before they become expensive repairs. Digital vehicle inspections allow technicians and drivers to flag concerns and generate work orders quickly.
- Conduct pre- and post-trip inspections regularly
- Digitize inspections for faster communication and recordkeeping
- Track recurring issues across asset types to guide PM improvements
Train drivers on what to look for during inspections – they’re your frontline for identifying developing problems.
As a fleet manager, talk to your drivers; if they’re seeing lights coming on, if they’re smelling things, if they’re hearing things, if they’re feeling things, that’s going to be your best source of information. Don’t wait until a driver calls you, ‘Yeah, I’m on the side of the road. I’m in the middle of nowhere. The wheel came off.’ James Shelton, Jiffy Lube International
3. Monitor for manufacturer recalls
Recalls can impact asset availability, especially if replacement parts are delayed. Even well-maintained assets can be affected by recalls that require immediate service or part replacements. Staying proactive helps avoid unexpected shop time and ensures compliance with safety regulations.
Use tools like the NHTSA recall lookup tool or set up automatic alerts in Fleetio to regularly check for open recalls by VIN. This should be part of your ongoing PM workflow – not just a one-time task.
4. Create and manage work orders digitally
Digital work orders help streamline your PM workflow by making it easy to assign, prioritize and track maintenance tasks in real time.
- Convert failed inspections or service reminders directly into work orders
- Track labor hours, parts used and costs associated with each task
- Set deadlines and priorities based on asset criticality
Pro tip
Tracking work orders in a centralized maintenance system like Fleetio eliminates backlogs and keeps your team aligned on what's due and what's done.
5. Track third-party service efficiently
If your fleet relies on outside shops for fleet maintenance services, it’s essential to manage third-party maintenance with the same rigor as internal work.
- Use vendor integrations or portals to track service status
- Set approval thresholds to avoid delays
- Capture invoices and documentation in one place for future reference
6. Analyze PM data to make smarter decisions
The more data you track, the more strategic your PM program becomes. Use reports and dashboards to spot patterns, forecast needs and justify fleet decisions.
- Monitor costs by asset, system and service type
- Track downtime to measure the impact of PM
- Use maintenance data to inform asset replacement planning
Look for consistent issues (e.g., frequent brake repairs) that might reveal training needs or opportunities to spec better parts.
Preventive maintenance checklist to avoid downtime
By going through a fleet maintenance checklist every time a vehicle comes in for schedule preventive maintenance, you can often surface any other issues before it leads to a costly breakdown.
Checklists can be standardized across your fleet or customized based on asset type and usage. Consider adding fields for mileage, technician notes, and pass/fail flags.
Yes, this checklist could end up creating more work for your technicians, but it's more efficient to complete that work while the vehicle is already in the shop than having to schedule another time in the near future to bring it back in.
How Fleetio simplifies fleet preventive maintenance scheduling
Once your preventive maintenance (PM) schedule is in place, the next step is keeping it on track – consistently and automatically. That’s where Fleetio comes in.
Fleetio helps you automate your entire PM process by tying service reminders directly to usage data from inspections and telematics. When an asset is due for service, Fleetio notifies your team, creates a work order, and tracks completion—all in one system.
Here’s how Fleetio supports your schedule:
- Automatically updates meter readings through telematics or inspections
- Sends service reminders based on mileage, hours, or time intervals
- Centralizes service history for every asset
- Converts failed inspections into actionable work orders
- Provides dashboards to track compliance and performance
- Helps forecast future service needs with fleet reports
Most fleet software have similar functionalities regarding what the end result is, but it’s how you get to the end result and how user-friendly the interface is that’s important. Tom Rowlings, City of Cambridge DPW (Fleetio Customer)
With automated scheduling in Fleetio, you reduce the risk of missed maintenance and ensure your PM plan stays aligned with real-world asset usage.
The proof is in preventive maintenance
Keep your preventive maintenance schedule on track, on time, and on budget all under a single dashboard. Ready to go further?
Let’s schedule a demoFleet Maintenance FAQs
What is fleet maintenance?
Fleet maintenance refers to the scheduled and unscheduled care of fleet assets to ensure they operate safely, efficiently and reliably. It includes inspections, repairs and preventive maintenance tasks like oil changes and tire rotations.
What is fleet maintenance management?
Fleet maintenance management is the process of tracking, scheduling, and organizing repairs and preventive maintenance for all assets in a fleet. It helps reduce downtime, control costs, and extend asset lifespan.
What is fleet maintenance software?
Fleet maintenance software is a digital platform that automates maintenance scheduling, tracks service history, manages work orders, and provides insights to help fleet managers optimize asset uptime and reduce costs.
What is a PM schedule for maintenance?
A PM schedule (preventive maintenance schedule) outlines the planned service intervals for fleet assets based on time, mileage, or usage hours to prevent unexpected breakdowns and costly repairs.
What is a good maintenance program?
A good maintenance program prioritizes preventive maintenance, tracks asset performance, uses data to predict service needs, and leverages fleet maintenance software to automate tasks and minimize downtime.
What are preventive maintenance programs?
Preventive maintenance programs are structured plans to perform routine maintenance at regular intervals to keep assets running smoothly, avoid unexpected repairs, and extend asset lifespan.
What are the 3 main types of maintenance?
The three main types of maintenance are preventive maintenance (scheduled servicing to prevent issues), corrective maintenance (repairs after a failure), and predictive maintenance (forecasting service needs based on data and trends).
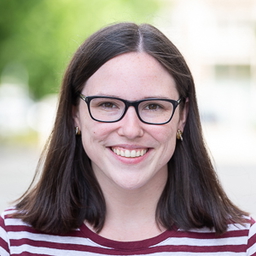
Content Marketing Specialist
Laura Flowers is the Content Marketing Specialist at Fleetio. When she’s not blogging, you can find her reading on the couch with her cat or in the studio tap dancing.
LinkedIn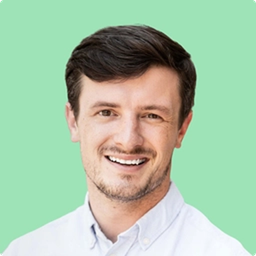
Director of Fleet Content, Fleetio
Zach Searcy is the Senior Content Marketing Manager at Fleetio with more than 5 years of experience in the automotive and fleet industries. His content creation days started in middle school when he and his friends began filming lightsaber battles to upload to a new website: 'YouTube.'
LinkedIn|View articles by Zach SearcyReady to get started?
Join thousands of satisfied customers using Fleetio
Questions? Call us at 1-800-975-5304